Evidence Collection and Root Cause Analysis by Accident? On your mark, get set… STOP!!

“Don’t collect evidence by accident!”
A phrase that I repeat often while teaching our TapRooT® Root Cause Analysis Method, along with…
Go Out And Look (GOAL)
I know, the phrases above may look like another safety/quality slogan of the day but are they? Maybe they should be the simplest guidance to increase the probability of not losing relative facts after an industrial injury, facility/property damage, environmental release, product defect, customer complaint or near miss/hit to any of the above.
Here is a list of issues that occur by not following the concise instructions above:
- Lost/Missing evidence
- Evidence spoliation (whether intended or not)
- Guessing driven by assumptions tied to past problems
- Regulatory Write Up for delayed incident reporting (extent and magnitude of problem not understand in time by not Going Out And Looking)
Why would any established industry, often overseen by a regulatory agency, have to worry about collecting evidence by accident or GOAL? Don’t many companies have procedures and work instructions on how to manage an industrial accident or regulatory write up? The latter question is where the problem resides. Actually, it starts before a major incident occurs.
Companies are good in many cases at handling major accidents and their evidence collection. What often drives what gets looked at is the company’s Incident Matrix. The matrix in many cases stops employees from Going Out And Looking and encourages last minute evidence collection by accident. Below is a typical matrix.
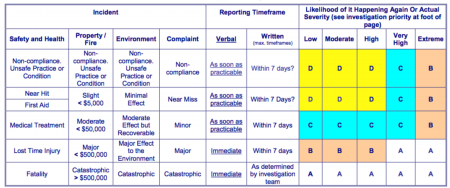
If the employee has “7 days?” or “as soon as practical”, what does that do to evidence collection delays or GOAL? What does that do to how the employee collects evidence and how the root cause analysis is performed? If the “big problems” have an investigation protocol, do the employees use the same protocol for the unsafe practice issues?
The process you create to manage investigation resources can hurt if not managed correctly.
For more thoughts on collecting evidence and the impact to the business based on your company’s own protocols, read the following….
New TapRooT® Essentials Book is Perfect for Low-to-Medium Risk Incident Investigations
You are just one Causal Factor from your next major Incident. Can you prevent it?
How Fast Can You Do A Root Cause Analysis (1 hour, 1 day, 1 week, 1 month)?
Top 3 Reasons for Bad Root Cause Analysis and How You Can Overcome Them…
3 Reasons a SnapCharT® is Essential to Evidence Collection
Starting Your Investigations: The Power of the SnapCharT®