5 Tips to Improve Your CAPA Program
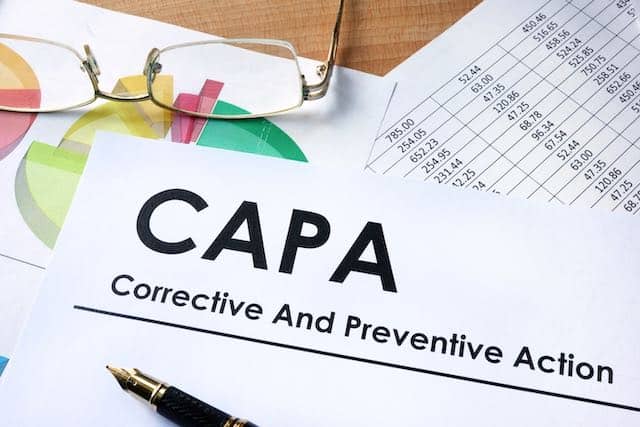
Improving CAPA
[Corrective and Preventive Action]
To improve your CAPA program, you need to address things that frequently cause CAPA Programs to fail. In this article, we will provide five tips to address five common problems. The problems are:
- Looking for root causes too early.
- Stopping the investigation before real, fixable root causes are identified.
- Throwing corrective actions at a problem.
- Using “easy” corrective actions rather than effective corrective actions.
- Failure to track corrective actions to completion and to check the effectiveness of the corrective actions.
Before we get started with these topics, let me explain that when using TapRooT® Root Cause Analysis, corrective actions are actions that will keep a problem from recurring. These are often called preventive actions in many quality CAPA systems. Also, the actions you take to immediately stabilize the facility and resume production are called “immediate actions.” In many quality systems, these are called corrective actions.
You might ask, why don’t we change our terminology to match the quality systems? Good question. First, this terminology is not standardized across industries and across professions (safety, quality, equipment reliability, patient safety, …). Thus, if we changed to match one industry, we would not match others. The term CAPA is used across many industries and is not used in others.
Second, we established our terminology in the mid-1980s. This was the same time that ISO management standards began to be developed and published (ISO 9000 was published in 1987 and followed by others published in the 1990s and later, including 9001, 9002, 9003, 14001, 18001, and 45001).
All standard terminology has a source, and the ISO standards source was the British Standards Institute. Where did our standard terminology originate? The Nuclear Navy.
So rather than changing the terminology that tens of thousands of TapRooT® Users use, we simply explain the difference and understand the roots of both terminologies.
1. Looking for Root Causes Too Early
This is a frequent problem that starts when people jump to conclusions.
We have written about the problem of jumping to conclusions before. Just click on the image above to review that article.
One thing we didn’t explain is that some root cause analysis tools start by asking, “Why?” This tends to cause people to jump to conclusions because they answer the why question with their current knowledge. After all, it’s hard to think of reasons you don’t understand. Most people have never had any human factors training. Therefore, most people don’t know much about why people make mistakes or how to prevent human error.
In the TapRooT® System, we start by trying to understand WHAT HAPPENED. We collect that information and organize it into an understandable visual sequence of events called a SnapCharT® Diagram.
Next, we identify the multiple (usually more than one) Causal Factors.
Once the Causal Factors are identified, each Causal Factor is analyzed using the TapRooT® Root Cause Tree® Diagram to find the Causal Factor’s real, fixable root causes. The Root Cause Tree® Diagram provides guidance (expert systems) to find the causes of human errors and equipment failures. Thus, the tree helps guide the analyst beyond their current knowledge. For more information about guided root cause analysis, see THIS LINK or the video below.
2. Stopping the Investigation Too Soon
One of the most frequent problems I have observed in quality investigations that are part of a CAPA System is stopping too soon. But I’m not the only one who sees this. The FDA often cites drug companies and food processors because their root cause analysis is inadequate. Often, the root cause analysis stops with a root cause of “human error” and doesn’t develop effective corrective actions.
These investigations that stop too soon often stop at what we call a Causal Factor. They don’t do the additional digging to find correctable root causes (as TapRooT® Users do when they use the Root Cause Tree® Diagram).
That’s why guided root cause analysis (explained in the video above) is so important.
3. Throwing Corrective Actions at a Problem
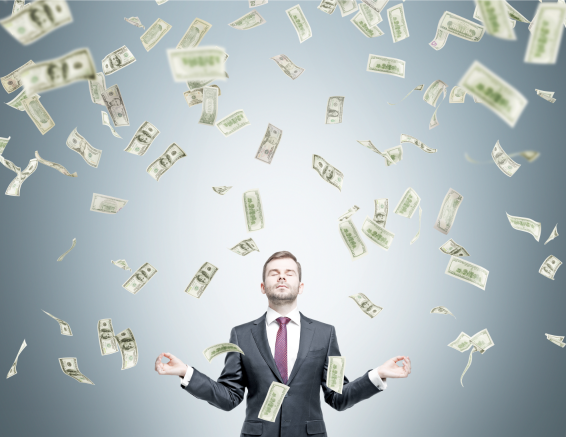
When investigators don’t find root causes, they can be tempted to throw common corrective actions (and money) at the problem. These common corrective actions include:
- Training
- Discipline (starting with counseling the operator to be more careful and progressing up to firing them)
- Writing procedures (or making procedures longer with more warnings)
In addition, investigators often recommend “re” corrective actions. For example:
- “re”-train
- “re”-mind the employee
- “re”-view the procedure
- “re”-write the procedure
- “re”-evaluate
- “re”-emphasize
- “re”-place a part
- “re”-qualify
- “re”-peat anything
If they didn’t work the first time, why will these “re” corrective actions work when you do it again? Yet, investigators often throw many of these “re” corrective actions at the problem. After all, the more, the merrier!
The TapRooT® System has guidance – the Corrective Action Helper® Guide (or the Corrective Action Helper® Module in the TapRooT® Software). This helps the investigators (or anyone developing corrective actions) think of effective corrective action ideas. This makes for fewer but more effective corrective actions.
4. Using “Easy” Corrective Actions Rather Than Effective Corrective Actions
This is similar to the previous problem, except the investigator is more judicious (recommends less) about recommending corrective actions that aren’t effective.
These “easy” corrective actions are among the weakest Safeguards on the hierarchy of Safeguard effectiveness shown below…
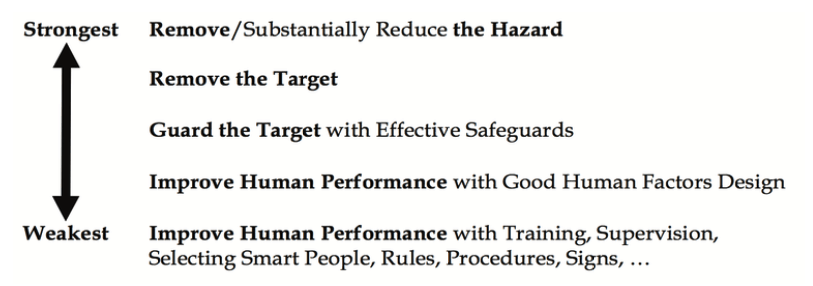
This led us to develop a four-category list of corrective actions based on a best practice of one of our TapRooT® Users:
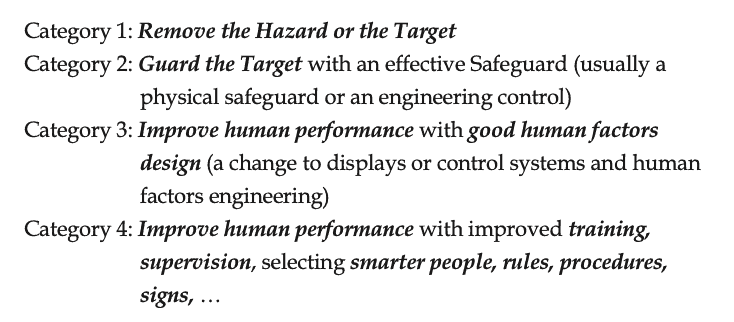
For high-consequence incidents, you should be using Category 1 or 2 corrective actions.
For more about corrective action development, we recommend attending the 5-Day TapRooT® Advanced Root Cause Analysis Team Leader Training or reading the TapRooT® Root Cause Analysis for Major Investigations book.
5. Failure to Track and Check Corrective Actions
What could be worse than not even doing what you said you would do?
I find it hard to believe that any effective management system would NOT include a good method to track corrective actions to completion and then validate the effectiveness of the corrective action before the investigation is closed out. Perhaps not every corrective action needs validation, but every corrective action needs to be tracked to completion.
But what do we find? Companies don’t have effective systems to track to completion (verify and validate their corrective actions). And what do we find when the system to verify the completion of corrective actions is substandard? Many (maybe even a majority) of the corrective actions recommended and approved by management were never completed.
Do you have a systematic process to verify and validate your corrective actions? We have built a process into the TapRooT® Software.
Time to Improve?
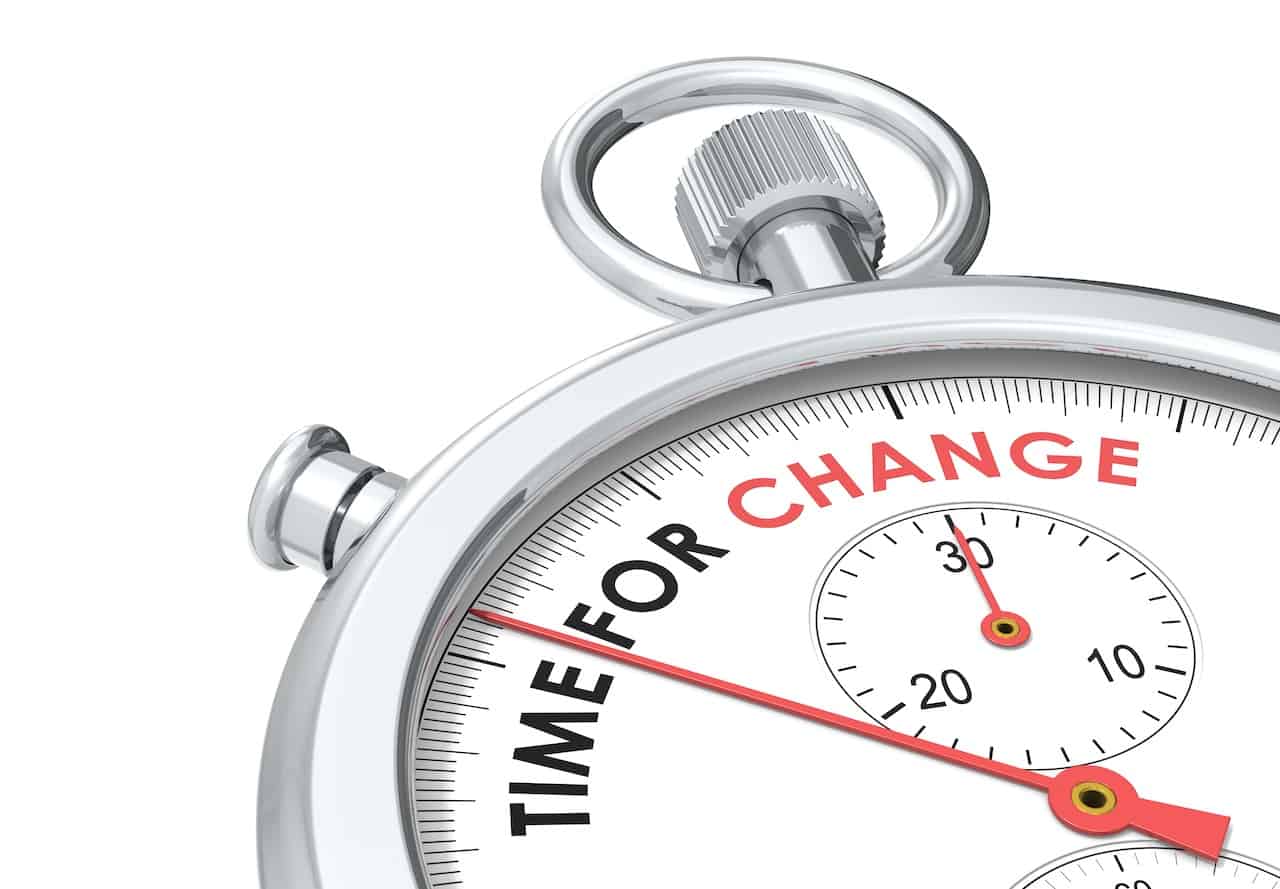
Improvement means change.
If you think that any of the five common problems listed above sound familiar, then you need to change (improve) your CAPA System. Maybe you should implement TapRooT® Root Cause Analysis or improve your use of the TapRooT® System. We would be happy to help you develop a “Roadmap to Success.” Find out more by calling 865-539-2139 or drop a note about developing a Roadmap to Success by CLICKING HERE.
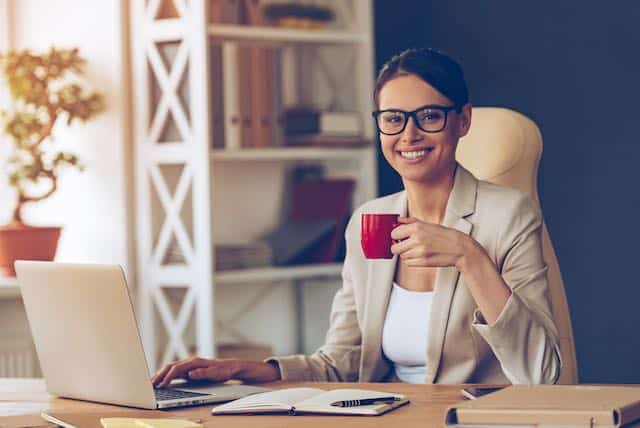
Also, consider attending the Better Improvement Programs and CAPA Track at the 2024 Global TapRooT® Summit.
When and where is the 2024 Global TapRooT® Summit?
The Summit is on May 1-3, 2024. The pre-Summit Courses are on April 29-30. Both are being held at the Horseshoe Bay Resort near Austin, Texas.
Attending the Summit will help you make your CAPA Program world-class and help you and your management meet your quality improvement goals.
Don’t wait! REGISTER for the 2024 Global TapRooT® Summit at the Horseshoe Bay Resort today.
