Does Your Corrective Action Program Need Corrective Actions?
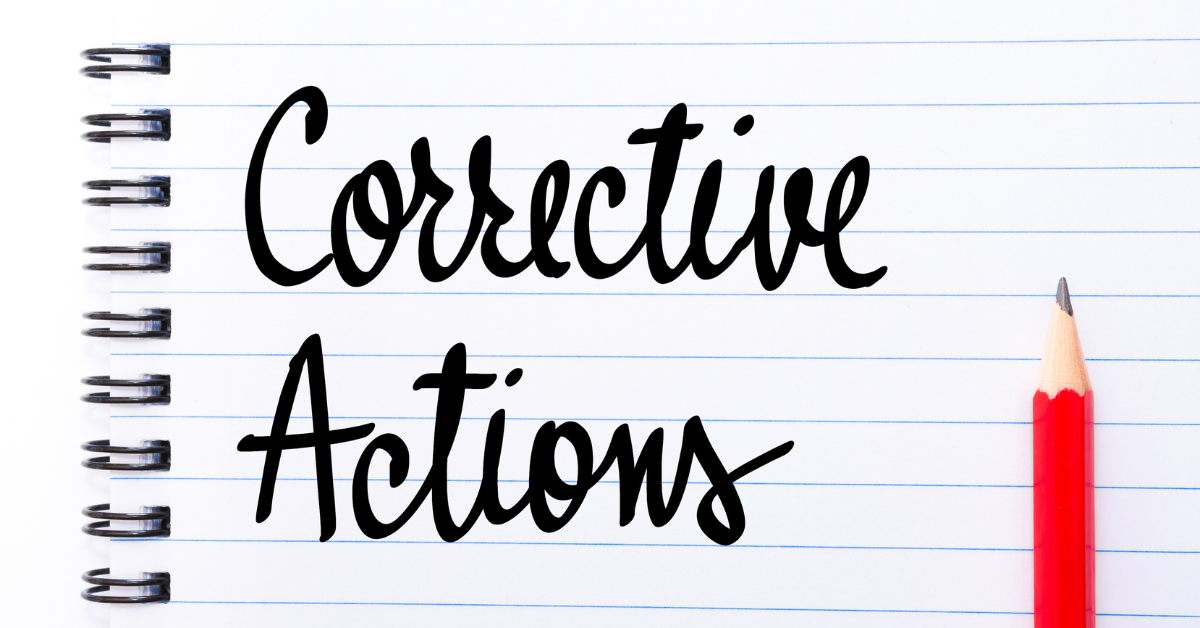
Many organizations come to us when they get frustrated by repeat incidents. This is sometimes a symptom of the corrective action program. We find that repeat incidents happen because corrective actions don’t fix the root causes or system weaknesses identified during the investigation and RCA process.
Root causes are the absence of best practices or knowledge that allowed the problem to exist.

Maybe you simply never faced the problem before so your systems were missing a best practice or knowledge. Management can’t predict and prepare for every eventuality. So when you do find a system weakness, your corrective actions should introduce missing best practices or knowledge that will improve your systems so you don’t have to worry about the problem reoccurring.
Every investigation and corrective action should lead to continuous improvement!
But sometimes the system’s weakness is the corrective action program itself and the missing knowledge or best practices you want to introduce into your systems never get there.

Solutions to your Corrective Action Program Problems
If that’s the case, the TapRooT® RCA tools will help you identify the system weaknesses or root causes of the corrective action program’s problems. The TapRooT® Root Cause Tree Dictionary will provide the expert questions you should ask during your investigation and RCA to help determine if your corrective action program does indeed need attention. As you answer the questions based on the evidence you found during the investigation, you will select or eliminate root causes based on solid evidence. That allows you to easily go through the process and defend your findings to anyone. TapRooT® is an evidence-based RCA process. You can highlight the evidence that allowed you to select every single root cause found. That cuts out a lot of second-guessing or wasting resources fixing root causes that don’t exist.
Eliminating root causes are as powerful as identifying them!
After you use the TapRooT® Root Cause Tree and Dictionary to identify the system weaknesses in your corrective action program, TapRooT® will also give ideas on how to implement the missing best practices or knowledge into your systems. Our Corrective Action Helper® Guide is full of ideas, best practices, knowledge, and references to help you create a more impactful corrective action.
The TapRooT® Process will also help you build out a formal process for introducing corrective actions by creating implementation tasks, verification tasks, and validation tasks that can be tracked and trended for effectiveness.

SMARTER Corrective Actions
During the implementation phase, we train on the use of a SMARTER format for creating your corrective actions. Whoever is assigned to implement the corrective action won’t have to guess how to implement the corrective action or be able to take the path of least resistance when implementing. Clarity creates confidence and when people are confident, they perform better.
The next step in introducing corrective actions should be having someone else verify that the corrective action was implemented well. Trust but verify. Build a task for someone to go out and see that the specific plan was followed and the corrective action did in fact introduce the missing best practice or knowledge into the system. This person should come back to the team and verify that the corrective action was implemented exactly according to plan. There should be some type of measurement in the verification plan to ensure the findings are objective.
Just because the corrective action was implemented correctly, it doesn’t guarantee we got it exactly right. Someone should be assigned to go out and see if the problem the corrective action was supposed to solve is still happening. If the problem is still happening, there is still the risk of a repeat incident. Corrective actions shouldn’t be closed out until after this step if the consequences of a repeat incident are not tolerable. The good news is that there is still time to adjust the corrective action at this point.
We certainly don’t want to wait to find out our corrective action wasn’t effective because the problem that was supposed to be fixed caused a repeat incident!
If you have any questions about the TapRooT® Training or RCA tools, I’d be honored to provide a demo via a web meeting. Please contact me at marcus@taproot.com.