Foreword of the New Book – Stopping Human Error – by Mark Paradies
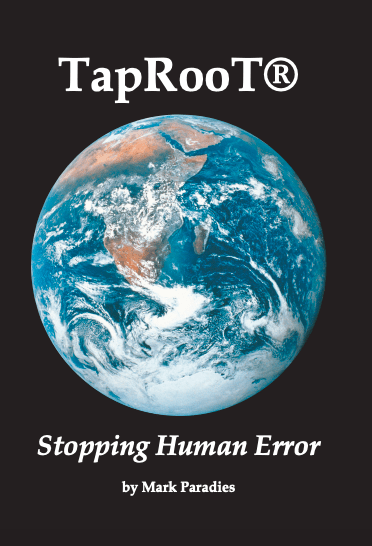
Foreword of New Book – Stopping Human Error
What’s the new book, Stopping Human Error, all about?
Here’s a sample of the book (the Foreword) for you to read and get an idea…
FOREWORD
All men make mistakes,
but only wise men learn from their mistakes.
Winston Churchill
Why Is This Book Important?
What is the cost of human error? Let’s look at one example…
According to The Guardian, one of the most expensive accidents – the Deepwater Horizon explosion, fire, and oil spill – cost BP over $65 billion (The Guardian, “BP’s Deepwater Horizon Bill tops $65bn,” January 16, 2018). Of course, the cost in dollars doesn’t account for the 11 people who lost their lives. On top of that is the environmental damage that will never be entirely known.
Let’s put the cost of that accident ($65 billion) in perspective. First, ExxonMobil bought XTO Energy at the height of the oil boom for $41 billion. Also, besides the direct costs, BP’s stock lost about one-half of its value. Nine years after the accident, the stock had not regained its price before the accident.
Now consider the cost to the oil industry. Drilling for oil in the Gulf of Mexico was suspended by the US government for all companies from July of 2010 until October of that year. Even after that, it took months for many rigs to resume drilling. Some were moved to other areas and drilling was never resumed.
The cost of one major accident is small compared to the cumulative cost of all human errors. Start thinking about the cost of these errors:
- 250,000 people die each year in the United States due to errors by healthcare professionals (The British Medical Journal, “Medical error – the third leading cause of death in the U.S.,” May 3, 2016).
- $871 billion per year of costs due to motor vehicle accidents in the United States, according to a study released in 2014 by the National Highway Traffic Safety Administration (the number includes lost economic and societal costs, such as productivity, court costs, medical costs, emergency services, insurance administration costs, and property damage).
- $37 billion per year is the cost of “misunderstandings” for US and UK companies, according to a white paper published in 2008 by IDC, a global analyst firm (IDC Research, “$37 Billion: Counting the Cost of Employee Misunderstanding,” Framingham, MA, 2008).
- $165.6 million was the cost to NASA of a Lockheed Martin engineer confusing feet and meters (metric conversion) and the resulting loss of the Mars orbiter.
The cost of errors to other companies or society is interesting, but what does this cost mean to you and your company? Let’s make these costs personal. What are the costs to your company of human error? For example, what are the costs of:
- Fatalities and lost time injuries?
- Needless equipment repairs?
- Lost production due to equipment stoppages?
- Rework of manufactured products?
- Returned products due to quality issues?
- Regulatory fines or stop-work orders?
- Delays in permits/government approvals?
- Production upsets?
- Lost business due to schedule slippage/late shipments?
- Project delays and rework due to construction mistakes?
- Replacing people who quit after an accident and training their replacements?
- Bad press after accidents (reputation loss)
- Insurance premium increases?
Calculate the costs to your company of human errors.
Is stopping human error worthwhile for your company? My guess is YES! That is why we wrote this book – to provide readers with proven techniques to “stop” human errors that cause major accidents and to use those same techniques to improve quality, equipment reliability, regulatory performance, human reliability, schedule performance, production, and service, as well as reducing costs.
Please use this book to help your company achieve human performance excellence. Read on to find out how…
How Should You Use This Book?
This book is a reference. You can read the whole book (just like a novel) or you can just skip to the parts that you need.
But how do you know the parts of this book you need? Here is some guidance.
Get started by reading Chapter 1, Can We “Stop” Human Error. This chapter is for everyone.
Next, review the focus of Chapters 2-6 (outlined on the next page). You can jump into any chapter that you think you need.
Finally, Chapter 7 is for anyone developing a human performance improvement program. It provides ideas to develop your program and a sample program with the results they could achieve and the continuous improvement that they plan. For a complete understanding of Chapter 7, you may need to read Chapters 2-6 to understand the techniques that are referenced before you start reading Chapter 7.
Now, for a quick review of Chapters 2-6…
CHAPTER 2: Human Factors Design Best Practices
This chapter outlines best practices that should be applied to any new facility or modifications to existing facilities. It starts with Human Engineering best practices (Section 2.1) but also includes:
- Communication Best Practices (Section 2.2)
- Procedures Best Practices (Section 2.3)
- Training Best Practices (Section 2.4)
- Work Supervision Best Practices (Section 2.5)
- Management System Best Practices (Section 2.6)
- Quality/Inspection Best Practices (Section 2.7)
CHAPTER 3: Proactive Techniques for Finding Human Error-Likely Situations
Chapter 3 covers proactive techniques to spot error-likely situations before accidents happen. These techniques include:
- Technique for Human Error Rate Prediction (THERP)
- Failure Modes and Effects Analysis (FMEA)
- Fault Trees
- Pre-Job Hazard Analysis using TapRooT®
- Proactive TapRooT® Root Cause Analysis For each technique, the chapter provides:
- The technique’s advantages and disadvantages
- References for more in-depth learning
CHAPTER 4: Strategies to Stop Human Error
This chapter provides a review of best practices used in high-reliability industries to achieve operational excellence. It starts with Safeguard Analysis, Defense-in-Depth, and Mistake Proofing. It then reviews techniques taught in Human Performance (Hu) or Human Performance Technology courses. These techniques include:
- Procedure Use/Adherence
- Place Keeping
- Independent Verification
- Three-Way Communications
- Pre-Job Brief/Personal Safety Assessment
- Observation and Coaching
- Post-Job Brief
- Concurrent Verification
- Questioning Attitude
- STAR
- Time Out (Stop When Unsure)
- Attention to Detail
- Management of Change
- Error Traps and Precursors
- Validate Assumptions
- Do Not Disturb Sign
- Conservative Decision-Making
For each of these tools, the chapter explains:
- How the tool works.
- When the tool is used.
- If it is related to root causes listed on the Root Cause Tree®.
- Where (what industry) the tool has been applied.
- Research that supports (or fails to support) use of the tool.
- Problems with application of the tool.
- If the tool required any special management support.
- If we recommend using the tool.
CHAPTER 5: Using TapRooT® to Analyze Human Error
This is the chapter that TapRooT® Users know the most about. However, for those unfamiliar with TapRooT® or those who haven’t been to TapRooT® Training since 2015, this chapter provides an overview of how advanced root cause analysis is applied to analyze human errors.
This chapter IS NOT a replacement for learning the TapRooT® Root Cause Analysis System. We believe TapRooT® Root Cause Analysis is the most important tool in your human performance toolbox. Therefore, we recommend reading the other TapRooT® Root Cause Analysis Books (reference at the start of Chapter 5) and attending a TapRooT® Root Cause Analysis Course (preferably the 5-Day TapRooT® Course for those who are interested in solving complex human error- related incidents). For more information about TapRooT® Root Cause Analysis Training, see www.taproot.com/courses.
CHAPTER 6: CHAP – Critical Human Action Profile
CHAP is an optional TapRooT® Tool that can be applied proactively to identify potential human factors issues. The technique is based on the human factors tool called Task Analysis.
That’s it! Five chapters packed with techniques to help you stop human errors (or at least, improve human performance), plus two chapters that explain stopping human error and developing your human performance improvement program.
Thanks to Those that Helped and Will Help
One final note. This book isn’t perfect. The field of human performance improvement is always progressing and there will be new ideas and perhaps better examples of ways to improve after this book is published. Rather than waiting for perfection, we thought it was important to get this book to you NOW!
However, to make the book as useful as possible, we requested and received reviews from our staff, our contract instructors, and the TapRooT® Advisory Board. These reviews provided helpful ideas that made the book better. Thanks to all who contributed.
However, we know that even as the book is published, you, the reader, will have suggestions to make it even better. You might have great pictures of bad human factors examples. We would like to hear from you. For those who use old fashioned communications, please write:
Mark Paradies
System Improvements, Inc.
238 South Peters Road, Suite 301 Knoxville, TN 37923
Or e-mail Mark Paradies at info@taproot.com. Thanks in advance for your suggestions and pictures.
Order Your Book at this Link
https://store.taproot.com/book-10-taproot-stopping-human-error
Get Your Book with this Course
https://store.taproot.com/search?q=Human+error