Mistakes at TVA Reactors Results in Safety Stand Down
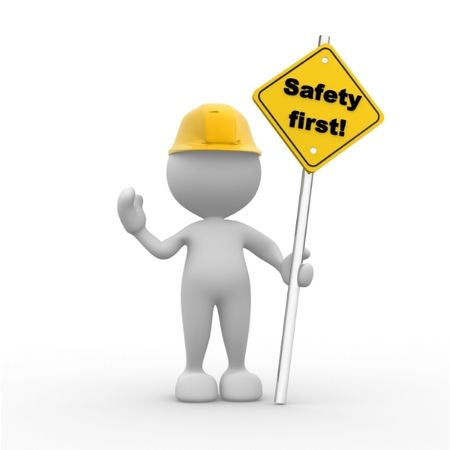
Ah, the ever-popular safety stand down. If people make mistakes, it must be time to have one.
A story in the Atlanta Business Journal says:
“A TVA spokeswoman told the Chattanooga Times Free Press that the construction ‘stand down’ ordered to start at noon Wednesday was to continue ‘until the errors discovered are clearly communicated to all personnel.'”
Will communicating the “errors” really improve performance?
A TVA spokesperson said:
“TVA had not yet determined if the mistakes were due to carelessness but a ‘root cause analysis’ was being conducted.“
Carelessness as a potential “cause”?
TVA’s top executive, Tom Kilgore, said:
“When workers return to the site on Monday, they will join foremen and supervisors to review an error that occurred in December that had the potential for fatal consequences, and that was identified earlier this week at Watts Bar Unit 2. Also to be reviewed is a second incident that occurred this week which could have resulted in a severe injury or worse if it had happened under slightly different circumstances.“
That toolbox safety meeting shouldn’t take too long. From the report, they don’t know the root causes yet. All they seem to know is that two mistakes were made. I guess “foremen and supervisors” will just tell employees to “be more careful” and not to make errors. Then everything will be OK.
After that, employees will be willing to cooperate in an open and revealing root cause analysis. Especially when they know that management is looking for those who may have been careless.
We all know that the best way to keep people from being careless is to fire those who are found to be careless. If you fire careless people frequently, everyone will be happy and careful!
Another quote from the article:
“Nuclear Regulatory Commission Region 2 spokesman Roger Hannah said Friday that such work stoppages at nuclear plants are ‘not uncommon’ and probably occur every two or three years. Hannah said they are ‘not exclusive to the nuclear industry.’“
Wonder why they need a stand down every two or three years if they have an effective performance improvement program? I guess people need to be reminded to be more careful every two or three years.
Maybe we should just schedule these stand downs in advance? We could call it human performance preventive maintenance. Every two years, we would give people a day off to think about being more careful, and “Presto!” … no more human errors.
Or even better! Rate people on their potential for carelessness on a scale from 1 to 10. Then every year, fire the worst 10%-20% of the careless employees!
Do these actions sound like the Deming Red Bead Experiment to anyone? If you don’t know what the Red Bead Experiment is, see the following videos…
Now read these quotes:
NRC’s “…Hannah declined to speculate about any possible penalty for TVA. He said TVA would assess both nuclear safety and workplace safety issues.“
And …
“The problems were discovered in routine TVA inspections and follow heightened NRC scrutiny on other TVA nuclear plants.“
Ahhh… now we are getting to the “root cause” of the stand downs.
It will look like management is doing something.
Management would hate to look like they are doing nothing.
A stand down makes them look like they are doing something.
The more people stand down, the more dramatic the effect.
Thus, a stand down may keep the NRC from descending upon a nuclear utility.
If NRC management starts to believe that TVA has multiple troubled plants with multiple reasons for concern about human performance and reliability, that could result in a special inspection. A special inspection is bad. When multiple regulators descend upon a nuclear utility, they always find things that need to be improved. If too many areas need improvement, the NRC could order reactors shut down until the “culture” is changed.
An NRC-ordered shut down is bad news for the utility. “Changing the culture” can take years, cost millions of dollars, and result in many managers being fired. That’s much worse than the impact of a simple stand down for a few days. Thus, a stand down is a cost-effective way to keep the NRC happy – at least for a while – even if the stand down has no lasting impact on human performance.
Here’s what Deming has to say about this approach…
Is there a better approach?
How about honest recognition of mistakes big and small? Once the mistake is recognized, management could require a thorough, effective, advanced root cause analysis of any problem that could result in a significant impact on plant safety, personnel safety, radiation exposure, environmental performance, or plant performance. Management could then insist upon the development and implementation of effective (SMARTER) corrective actions. Part of those corrective actions could include effective communications about what happened and why it happened (the real root causes) to all employees impacted by the issue or the corrective actions.
What if you want to stop having stand downs (and the incidents that cause management to call for stand downs)?
Management needs to stop being REACTIVE by being PROACTIVE.
Management needs to shift from reactive root cause analysis to advanced PROACTIVE root cause analysis and stop problems before incidents happen. (We teach how to do this in our 5-Day TapRooT® Course.)
I’d recommend that TVA stop blaming workers (calling them careless) and start finding and fixing the real root causes of problems. Rather than a show stand down for the NRC, use effective advanced root cause analysis – both reactively and proactively – to improve performance and avoid issues that require stand downs every few years.
Show stand downs haven’t resulted in improved performance in the Nuclear Navy or the nuclear power industry (as evidenced by the fact that they are repeated over and over again), and the NRC should not accept them as effective management action. Rather, knee-jerk use of a stand down should be seen as a sign of weak management. Management that does not know how to improve human performance.
Avoid this scenario at your facility. Make sure that your management understands how to use advanced root cause analysis both reactively and proactively. Get your advanced root cause analysis program effectively implemented and then continue to improve it every year. And this advice is not just for nuclear utilities. Rather, it applies to every industry where mistakes may cause major accidents – oil, refining, chemical plants, aviation, railroads, shipping, pipelines, pharmaceutical manufacturers, mining, hospitals, …
Where can you learn best practices to improve root cause analysis and human performance? At the Global TapRoot® Summit. Don’t wait. Get registered today.