Pump Life Cycle Cost Analysis – Numbers Matter!
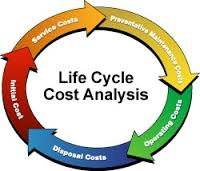
When designing spacecraft, there is a humorous (yet amazingly accurate) list of laws to keep in mind to ensure you are not going down the wrong path when developing spacecraft and their associated systems. Akin’s Laws of Spacecraft Design are a set of well-known nuggets that can be adapted to everyday life. But the one that I want to mention here is Akin’s Law #1:
1. Engineering is done with numbers. Analysis without numbers is only an opinion.
When you are looking at your pumping systems, and trying to decide on the best maintenance or repair strategy for a particular pump failure, you may have several options. For example:
– Should I just replace the failed pump with another identical pump?
– Should I replace it with a more efficient design?
– Is the current pump optimized for the system design?
– What other options are available for this repair?
– Why did it fail in the first place?
Life Cycle Cost analysis can be done after almost any failure to help you decide on the best repair strategy. This analysis includes things like the costs of the initial purchase, installation and commissioning costs, energy and operation costs, and maintenance costs. You can perform a relatively accurate cost comparison for various repair / replacement options so that you can make an educated decision on the best course of action. Pump Life Cycle Costs: A Guide to LCC Analysis for Pumping Systems is the result of a collaboration between the Hydraulic Institute, Europump, and the US Department of Energy’s Office of Industrial Technologies (OIT). It is definitely worth a few minutes to read through this and get a basic understanding of how to calculate the LCC of a particular installation or repair.
There were a couple of take-aways for me, neither of which was particularly surprising, yet both of which are important to keep in mind:
- Energy consumption is often one of the larger cost elements and may dominate the LCC, especially if pumps are run more than 2000 hours per year
- The cost of unexpected downtime and lost production is a very significant item in the total LCC and can rival the energy costs and replacement parts costs in its impact.
Which drives home the importance of a good root cause analysis to ensure that your failures (and therefore your downtime) are minimized, as the costs of these failures can rapid skew the entire LCC analysis. Don’t live with repeat or avoidable failures.