What works better than reminding people to “be careful?” or re-training them?
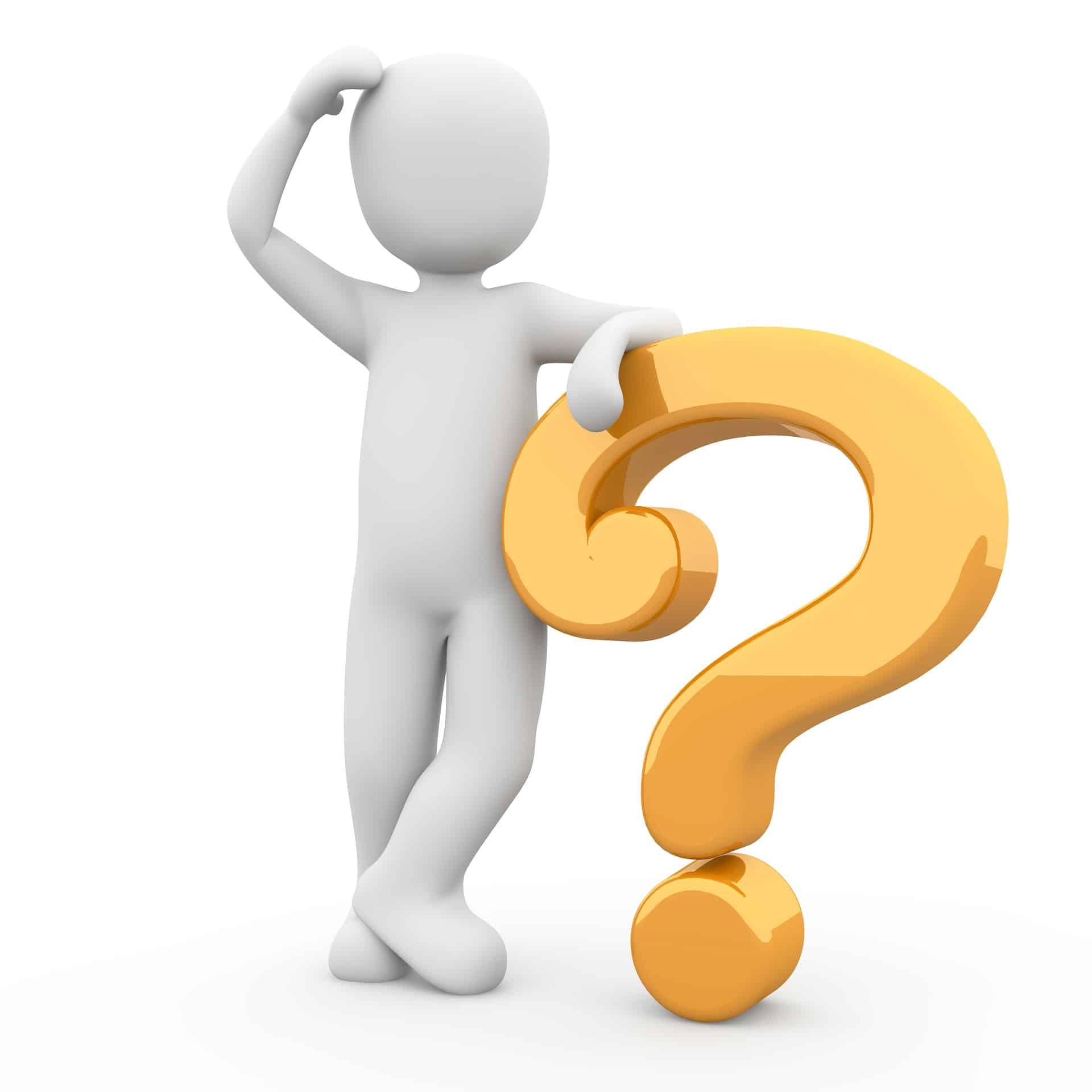
Zero error and six sigma levels of quality cannot be achieved by simply reminding people to be careful, watching training videos, or reviewing procedures once a year.
- How do restaurant, energy, and aviation employees achieve very low error rates on a consistent basis, while others who do less mistake prone work make significantly more errors each day?
- What approaches are used to obtain higher levels of policy and procedure compliance?
- How do the best organizations use work process and tool design to drive personal accountability on the job?
When incidents, recalls, sentinel events, production outages, customer complaints, and daily errors do happen, most problem-solving efforts typically produce a weak mix of corrective actions. In other words, the fixes often fail to prevent the errors that contributed to the problem from happening again. In turn, the same problems pop up again, often across multiple locations and work groups. Risk levels fail to be reduced, and process failures and costs remain high. Additionally, the bulk of the investigative effort was wasted.
Are you feeling this pain? Do you want it to end? Then join us to learn:
Best Practices in Mistake Proofing & Effective Corrective Actions
This workshop explores the common types of work process and tool design flaws that contribute to human error, including fixes that fail. It also gives you a coach and a practice field for learning to write more effective and sustainable corrective and preventive actions. Finally, this workshop gives you many best practices you can use to more effectively, and proactively, ‘mistake proof’ your workplace by fixing key work process and tool design flaws.
All two-day course participants will receive a course workbook and a copy of the facilitator’s latest book, “Error Proof – How to Stop Daily Goofs for Good.”
In this workshop, you will learn how to:
- Use best practice approaches for error proofing job tasks of any type
- Proactively identify and analyze opportunities for error in a systematic manner
- Better utilize the 32 NI root causes through benchmarking and best practice exploration
- Assess the relative strength of different corrective action options
- Write effective corrective and preventive actions that add value and can be sustained over time
- Capture and use process-level error rates as leading indicators of corrective action effectiveness
Kevin McManus developed and teaches this course. He serves as Chief Excellence Officer for Great Systems! and has taught more than 400 courses as an international contract trainer for the TapRooT® root cause analysis process. During his thirty-eight plus years in the business world, he has served as an Industrial Engineer, Training Manager, Production Manager, Plant Manager, and Director of Quality. He holds an undergraduate degree in Industrial Engineering and an MBA. He has served as a national Malcolm Baldrige Quality Award Examiner for eighteen years, and he is currently serving a three-year term on the national Judge’s Panel. He also writes the monthly performance improvement column for “Industrial and Systems Engineer” magazine, is an Institute of Industrial and Systems Engineering Fellow, and has been a member of IISE for thirty-eight years, His newest book, “The Ultimate Org Ergo Book – How to Build a Better Organization,” will be published in early 2019.
Register for *both* this course and the 3-day Global TapRooT® Summit, March 11-15, La Torretta Lake Resport & Spa, Montgomery, Texas. (Register)
Register for this special 2-Day course *only*, March 11-12, 2019, La Torretta Lake Resort & Spa, Montgomery, Texas (Register)
Learn more about the Summit.