First Step To Improving Asset Reliability
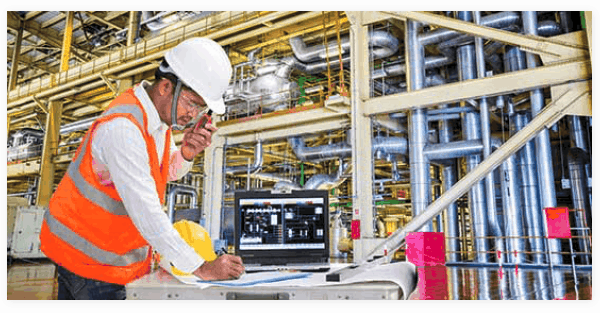
First Step to Improving Asset Reliability – Understanding Equipment Failure
Asset Reliability: Can you improve what you don’t understand? You might be lucky but the answer is usually,
NO!
I found that many people in the field working on equipment didn’t have a systematic way to troubleshoot equipment or process failures.
Sometimes they
- Guess what the problem is.
- Replace parts until the problem goes away.
- Call an expert to see what they think.
- Order a new piece of equipment to replace the old one without knowing the cause of the failure of the old one.
- Replace the cheapest part and hoped that works.
- Whack it with a hammer.
I used the last method today and IT WORKED! Will it continue to work in the future? I don’t know but I’ll keep the hammer handy.
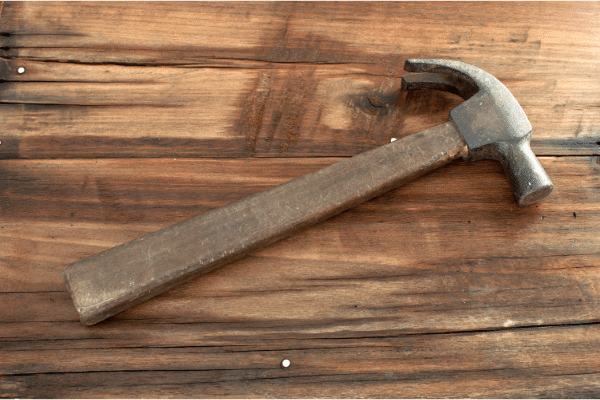
Some people used this troubleshooting method…
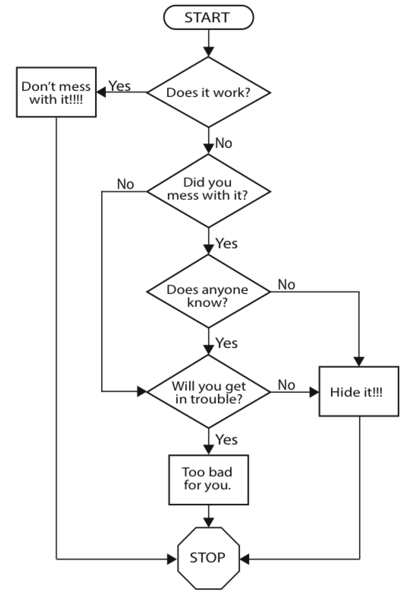
But if you end up in the “Too bad for you.” box, you might not enjoy the results.
Systematic Troubleshooting Methods
When I met Heinz Bloch back in 1997, we hit it off. I was an expert in root cause analysis and Heinz was an expert in equipment troubleshooting and reliability. Together we discovered that my knowledge of root cause analysis and his knowledge of equipment troubleshooting could fit together perfectly to create a systematic process for troubleshooting equipment and process failures and finding the root causes of failures.
We worked to perfect the system and named it Equifactor®. By 2000, we had the system integrated with the TapRooT® Root Cause Analysis System and had developed a course for equipment reliability professionals.
As we learned more about how troubleshooting was performed by field personnel, we modified the training and documentation to make the combined system easier to use. In 2015, we started writing a new book about applying Equifactor® for use by maintenance personnel.
That’s where we find ourselves now. We have an Equifactor® System, Software, and Training for Equipment Reliability Professionals, Maintenance Managers, and Maintenance Technicians that can help them systematically troubleshoot failures and, if they need to go further, find their root causes.
How Does Equifactor® Troubleshooting Work?
The process is quite simple but effective.
When you have an equipment failure, you apply the knowledge of Heinz Bloch to troubleshoot the problem. Heinz knowledge is contained in a set of easy-to-use troubleshooting tables.
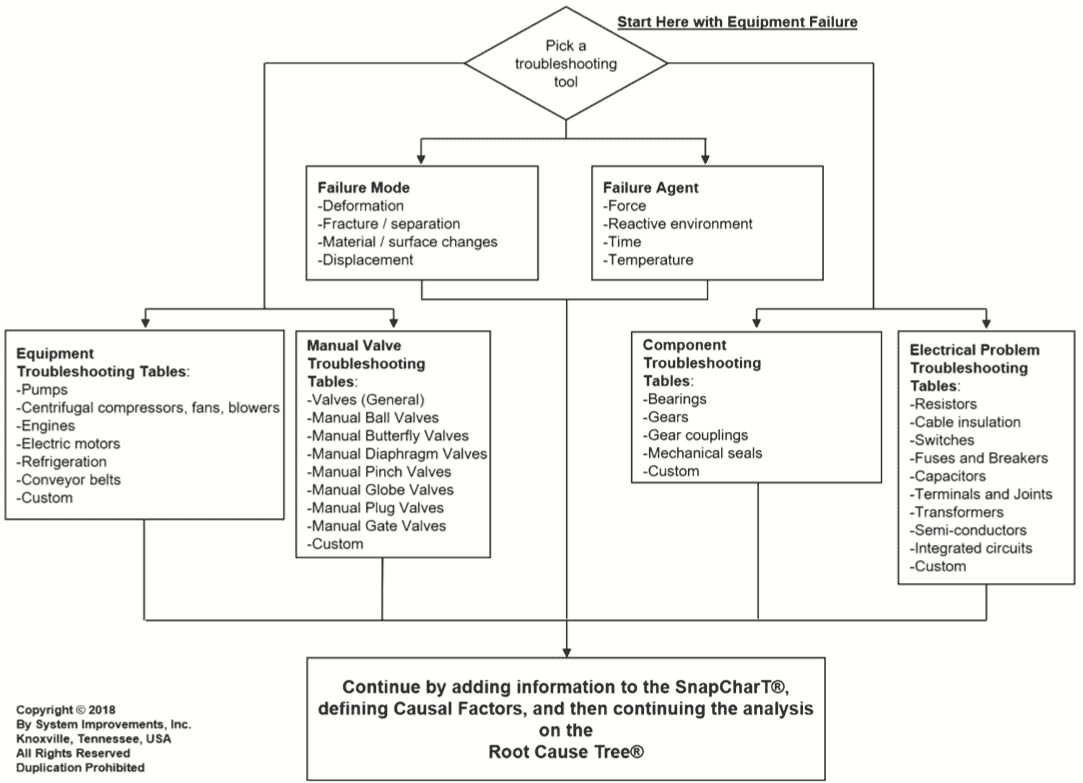
First, if you can identify the failed equipment or part, you use the applicable troubleshooting table.
For example, if a pump fails to supply enough water (less than rated capacity) you would identify the type of pump (in this case a centrifugal pump) and go to the Centrifugal Pump troubleshooting table. The table looks like this…
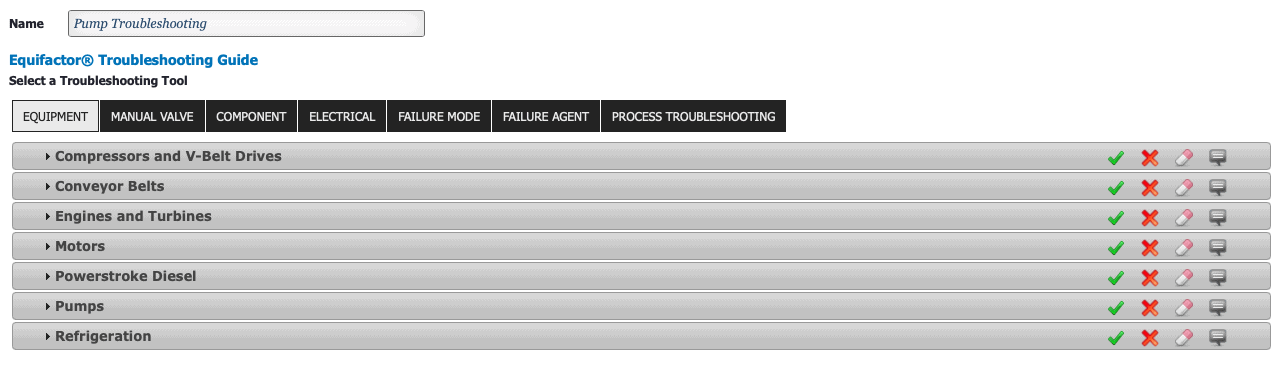
You would select the Pumps tab and then select the Centrifugal Pumps tab to see this troubleshooting table…
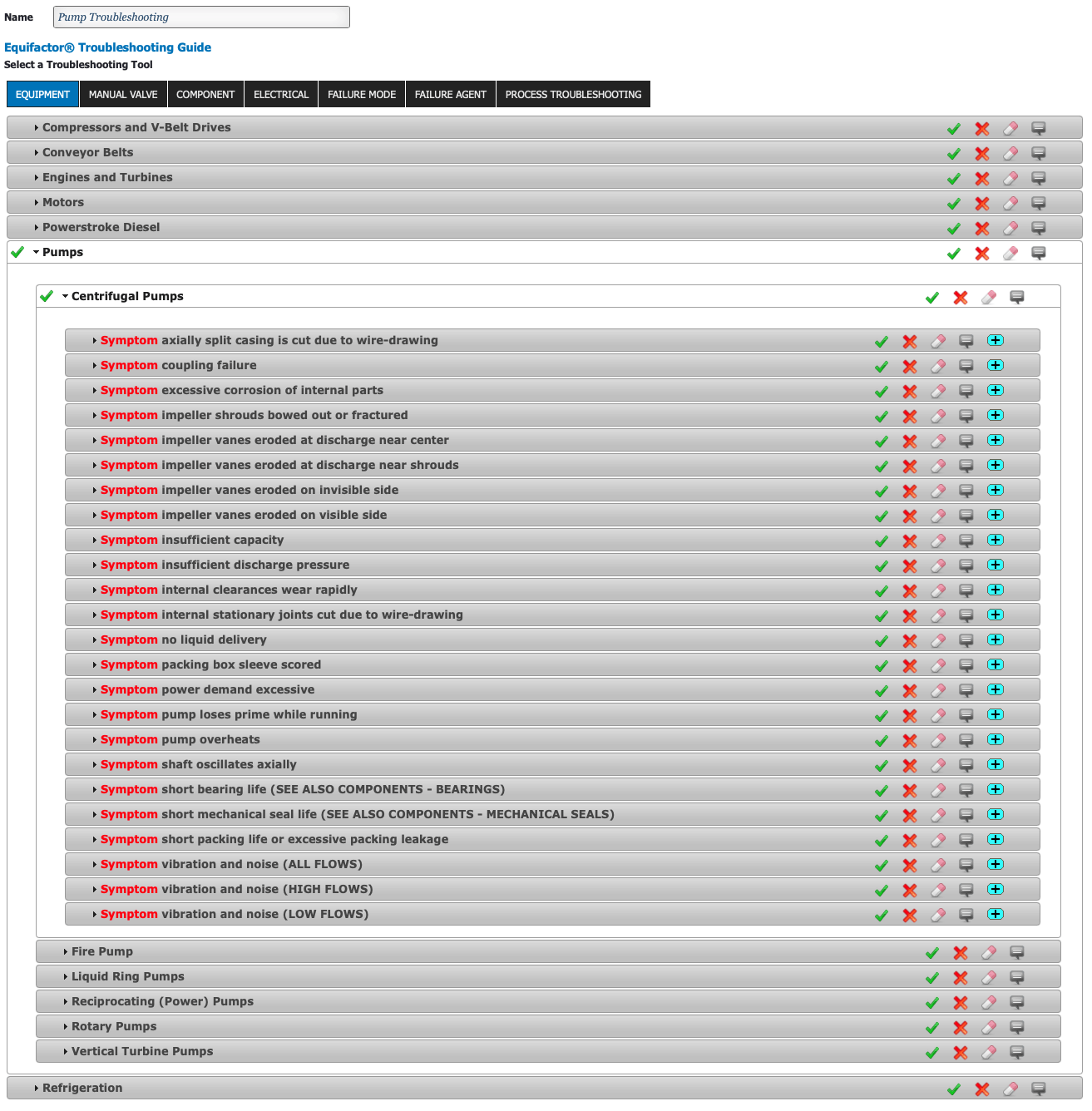
Next, you select a symptom that the pump is experiencing. In this case, it is Insufficient Capacity. When you click on that Symptom, you get this list of possible causes…
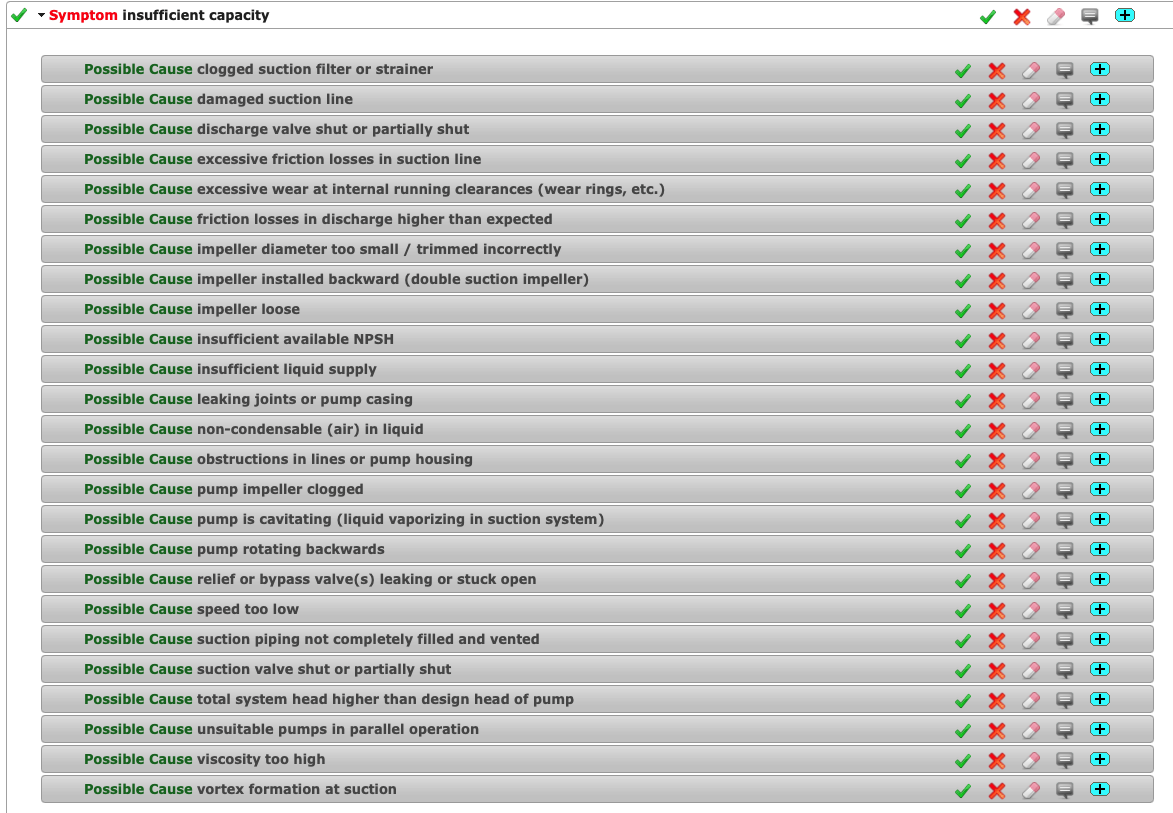
Now you are ready to perform a process of elimination and selection.
We suggest that you think through what you are doing to make the troubleshooting as efficient as possible.
In this example, one possible cause is that the discharge valve may be shut or partially shut. That’s an easy problem to check without disassembling the pump. And it would certainly make you feel stupid if you didn’t check this and went to more difficult Possible Causes before you checked this on.
But, in this case, the valve was open so we can eliminate this Possible Cause.
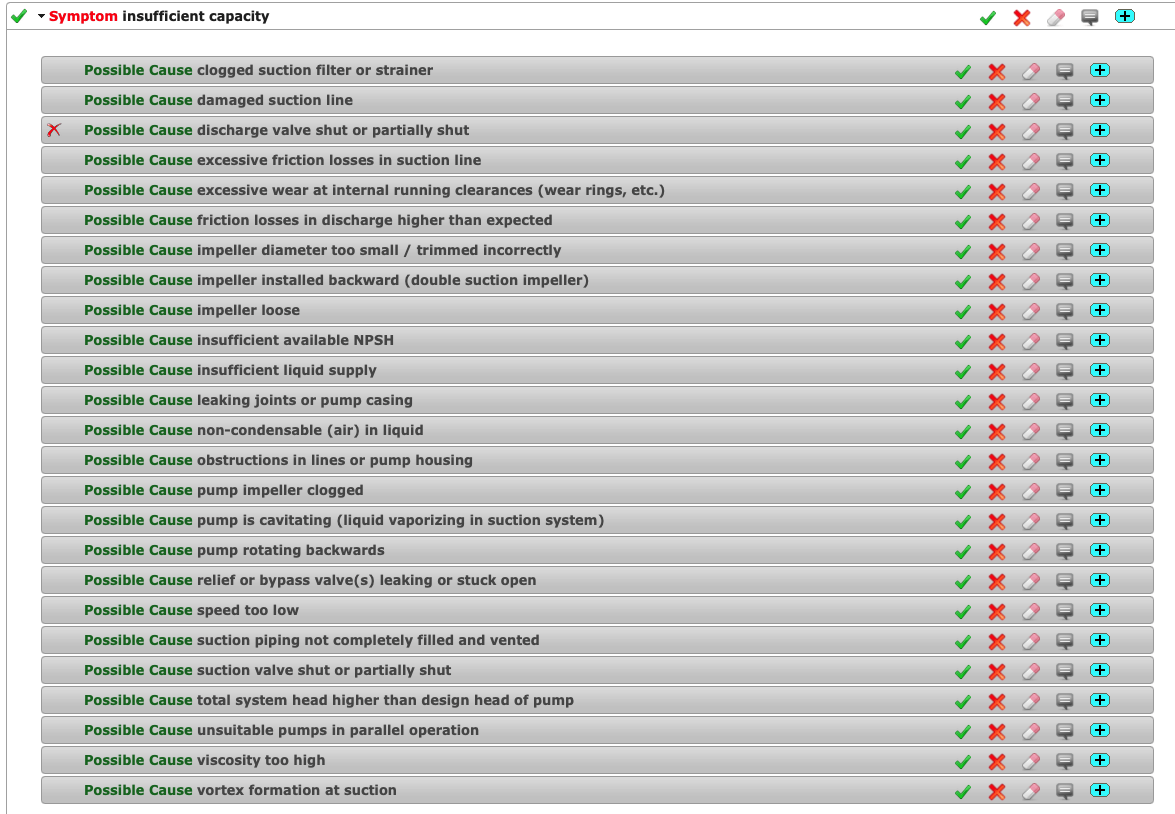
Once we have eliminated all the causes that can be eliminated without disassembling the system, we are left with hard work. But at least we have checked all the “easy” Possible Causes.
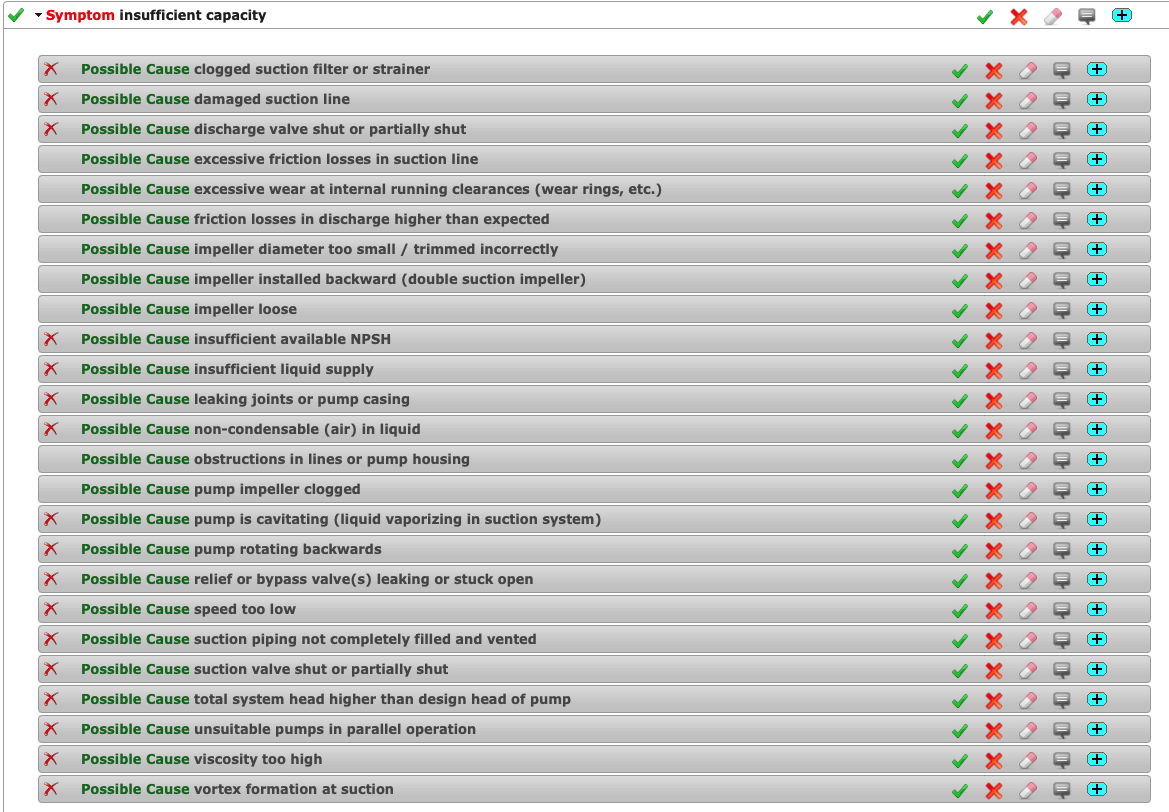
Next, we should make a checklist to follow while removing the pump from the system so that we collect all the evidence we need while taking the pump out of the system. We use the checklist to continue our troubleshooting until we find the Possible Cause that resulted in the equipment failure. In this case, we discover that the impeller was installed backward when the pump was rebuilt (it was a double suction impeller).
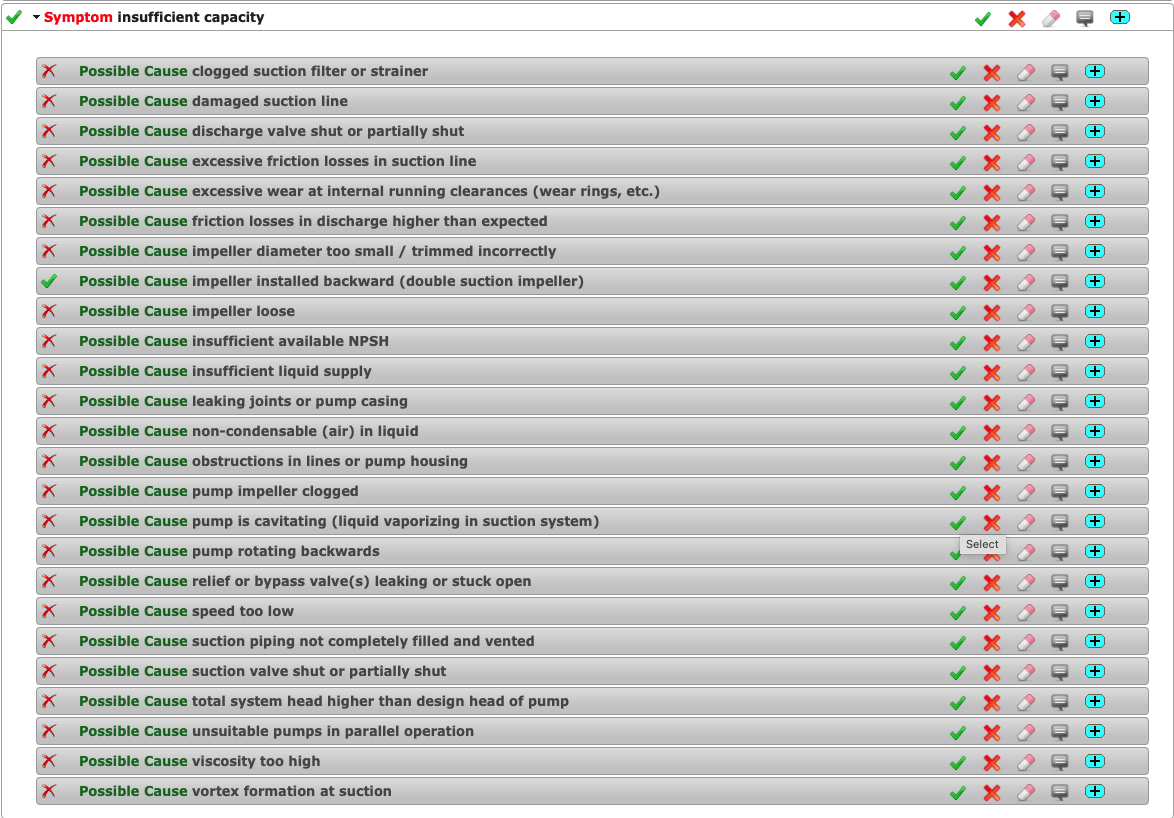
What do we do next? That depends. Obviously, we would reinstall the impeller correctly.
But, if we want to find out why (the root cause or causes) the impeller was installed backward, we would start an investigation using the TapRooT® Root Cause Analysis System. We would start by drawing a SnapCharT® Diagram of the process of the pump being rebuilt.
Find Out More About Systematic Troubleshooting and Root Cause Analysis to Improve Asset Reliability
If you need to improve asset reliability, you probably need to find out more about systematic troubleshooting and root cause analysis. Where can you learn more? At an Equifactor® Equipment Troubleshooting & TapRooT® Root Cause Analysis Course. Find out about what’s covered in the training at the link above.
Do you want to attend one of our public courses? See THIS LINK.
And if you want to have a 2-Day Equifactor® Equipment Troubleshooting & TapRooT® Root Cause Analysis Course at your site, CLICK HERE to contact one of our implementation specialists (or call 865-539-2139).
Don’t wait. Using a hammer probably doesn’t work for most equipment failures. Why not use a systematic troubleshooting process – Equifactor®.
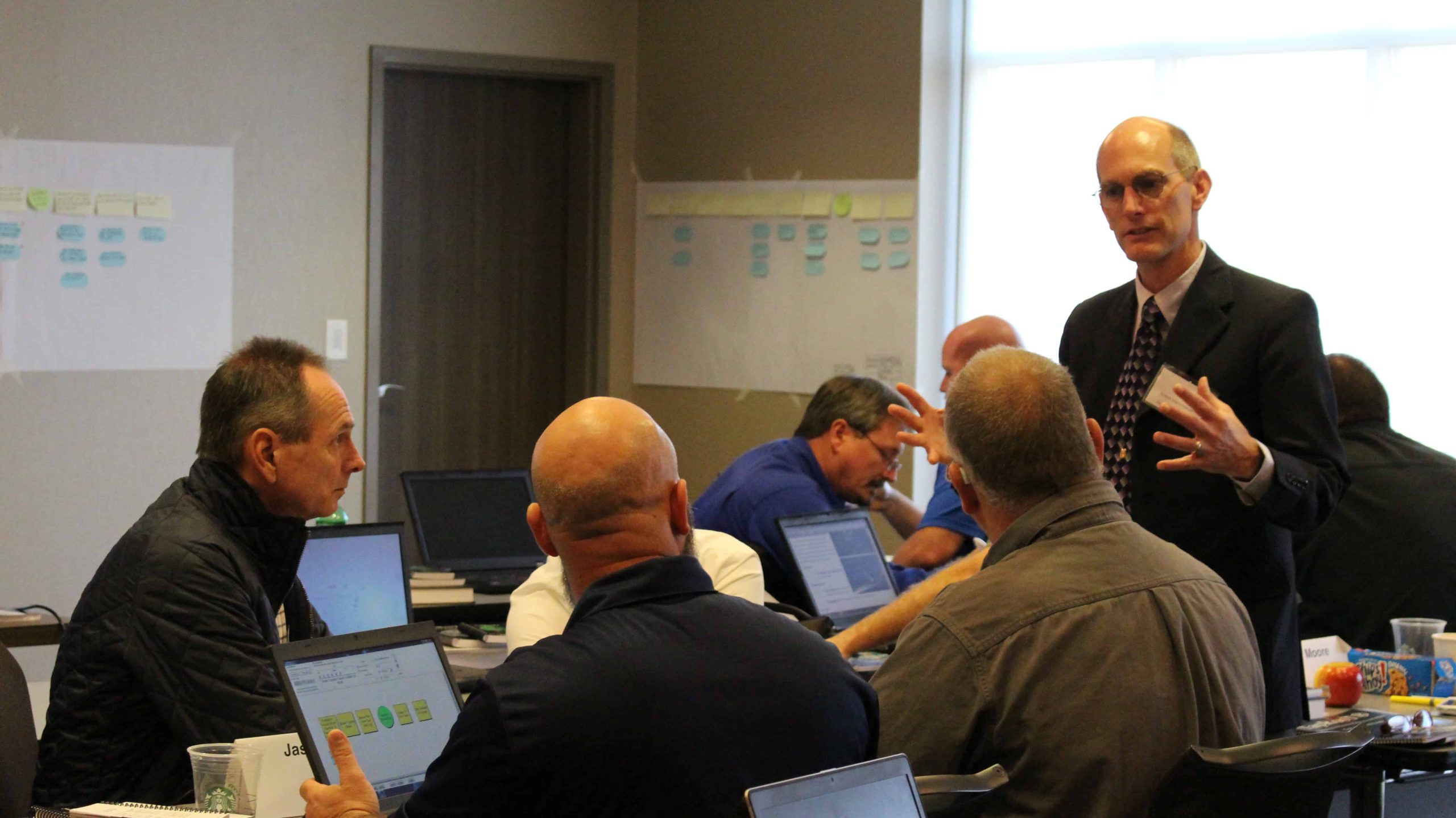
Here is the video we made about improving asset reliability…
If you would like to get a monthly newsletter about equipment reliability, asset reliability best practices, troubleshooting, and root cause analysis, just fill out the form below…