Troubleshooting and Root Cause Analysis of Equipment Reliability Problems
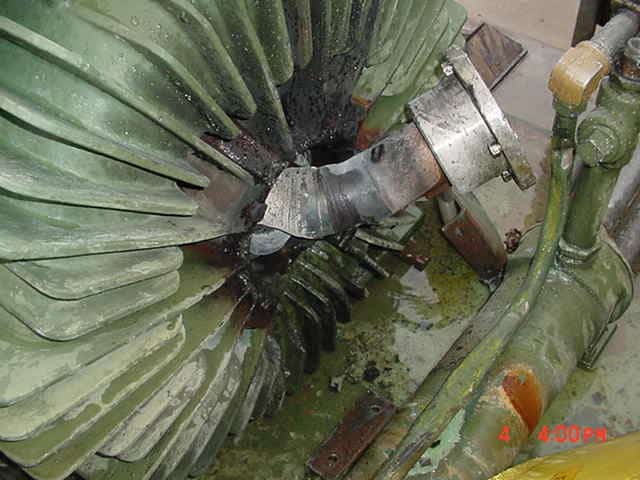
Finding Equipment Reliability Root Causes
What is the most common method of equipment failure root cause analysis? Is it…
- 5-Whys?
- Failure Modes and Effects Analysis?
- Fault Trees?
The real answer, observed in the field, is … GUESSING!
In other words, no formal root cause analysis is performed. The maintenance technician guesses an answer and tries a fix. This usually includes replacing a part. If the problem goes away (at least temporarily), the root cause has been discovered. If it does not go away, guess again!
This application of “guessing” as the primary tool for root cause analysis of equipment reliability and maintenance problems is probably the biggest challenge to achieving equipment reliability excellence.
Want to get beyond guessing? Then read on…
Troubleshooting IS NOT Root Cause Analysis
One of the first problems I observed in helping maintenance professionals find root causes was that they didn’t have the knowledge they needed to find the root causes. They were trying to find root causes BEFORE they completed troubleshooting the problem.
What is the difference between troubleshooting and root cause analysis?
Troubleshooting is trying to discover the physical or equipment cause of the failure. For example, if a pump is producing less than the rated flow, we might want to know why. If we discover that the impellor on a double volute pump was installed backward, we have completed the troubleshooting of the problem. We can reinstall the impeller the correct way, and the problem will be solved. But we haven’t found the root cause of the failure.
The Causal Factor is:
“Technician installs impellor backward.”
But that Causal Factor is just the start of the root cause analysis. We need to take that Causal Factor through the Root Cause Tree® Diagram to find the error’s root cause (or root causes).

The Root Cause Tree® Diagram systematically finds the root causes of equipment failures after the investigator troubleshoots the problem.
First, we troubleshooted the problem using Equifactor® Troubleshooting Techniques, and then we found the root causes using the Root Cause Tree® Diagram and the Root Cause Tree® Dictionary.

Equifactor® Troubleshooting
What are the Equifactor® Troubleshooting Techniques? They are troubleshooting tools developed by System Improvement based on Heinz Bloch’s troubleshooting techniques.
Here is a simple flow chart of the process:

The troubleshooting process includes troubleshooting tables for:
- Equipment (pumps, compressors, fans, blowers, electric motors, conveyor belts, …)
- Manual Valves
- Components (bearings, gears, gear couplings, mechanical seals)
- Electrical components
It also includes two techniques developed by Heinz:
- Failure Modes
- Failure Agents
This troubleshooting process is built into the Equifactor® Steps for Troubleshooting and Analyzing Equipment Failures shown below.

Troubleshooting using Equifactor® Techniques is taught in the 2-Day Equifactor® Troubleshooting and TapRooT® Root Cause Analysis Course.
The information gained during the troubleshooting is added to a SnapCharT® Diagram that displays what happened. The course also teaches how to use the SnapCharT® Diagram. An example of an equipment failure related SnapCharT® Diagram is shown below…

Notice that the Causal Factor (Mechanic installs impeller backward) is included on the SnapCharT®.
Root Cause Analysis
How do you find the root causes of the mechanic installing the impeller backward? That’s covered on the second day of the 2-Day Equifactor® Troubleshooting and TapRooT® Root Cause Analysis Course.
Would you like to learn how to troubleshoot equipment problems effectively and find root causes using the Root Cause Tree® Diagram? Then REGISTER for an upcoming public 2-Day Equifactor® Course. Or CONTACT US for a quote for a course at your site.
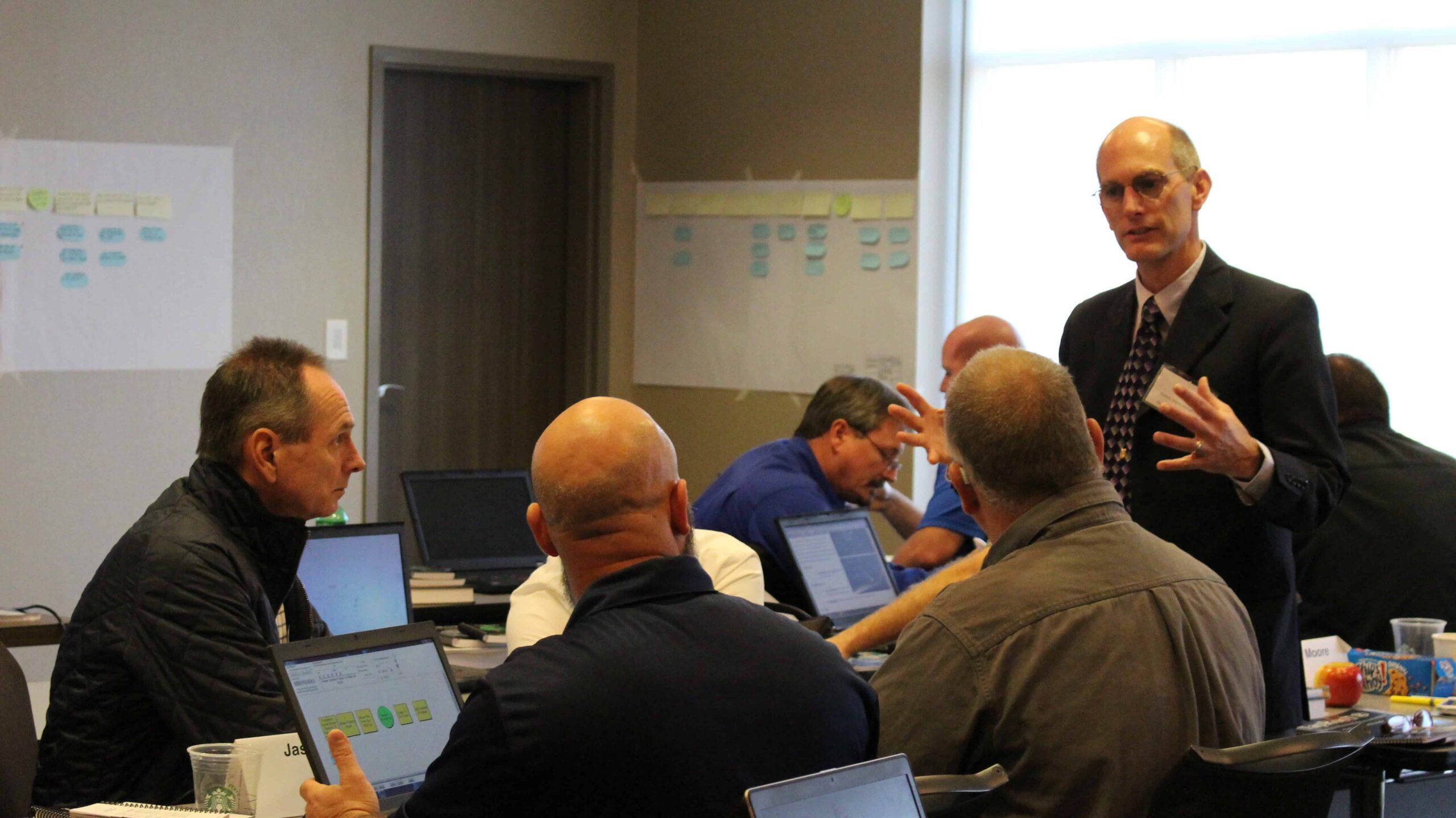