How to Make Team Incident Investigations Work
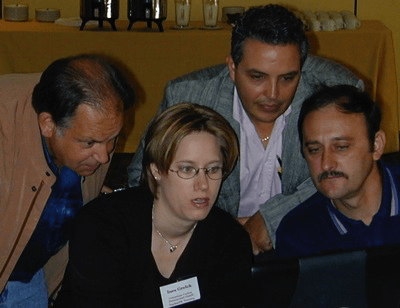
Why Use a Team to Investigate an Incident?
Before we discuss how to make a team incident investigations work, let’s ask the question:
Why would we use a team to perform an incident investigation?
First, team incident investigations are required for most process safety-related incidents at facilities covered by OSHA’s Process Safety Management regulation and the EPA’s Risk Management Plan.
Second, to put it quite simply:
Because two heads (or more) are better than one!
Why? Several reasons:
- A team’s resources can more quickly investigate an incident before the trail goes cold.
- For complex systems, more than one person is usually needed to understand the problem.
- Several organizations that were involved in the incident need to participate in the investigation.
- A properly selected team is more likely to consider all aspects of a problem rather than focusing on one aspect that a single investigator may understand and therefore choose to investigate. (The favorite cause syndrome.)

Factors to Consider to Make a Team Investigation Work
Investigating an incident using a team is different than performing an individual incident investigation. To make a team incident investigation/root cause analysis work, you need to consider these factors:
- Who to include on the team.
- The training required for team members.
- Division of work between team members
- Coordinating the team’s activities.
- Record keeping of the team’s efforts and meetings.
- Software to facilitate the team’s work.
- Keeping team members updated on the progress of the investigation (especially interview results) and maintaining a team consensus on what happened, the causal factors, and the root causes.
Selecting an Incident Investigation Team

The OSHA PSM regulation requires that the team include a member knowledgeable of the process and a contractor representative if contractor employees were involved in the incident.
Others you may include on the investigation team are:
- An engineer/technical assistant for technical/hardware expertise.
- A human engineering/ergonomics expert for human performance analysis.
- Operations/maintenance personnel who understand the work practices.
- An investigation coach/facilitator who is experienced in performing difficult incident investigations and root cause analysis.
- A record keeper to help keep up with meeting minutes, evidence documentation, and report writing/editing.
- A union rep.
- A safety or quality professional.
It may seem that there are many people you want on the team, but you should try to keep the team smaller rather than larger. Why? The bigger the team, the more difficult it will be to manage and reach a consensus. I usually suggest keeping the team to around five members or less.
Remember – not everyone involved in an investigation needs to be on the team. You may conduct interviews with operators, mechanics, supervisors, or managers and not include them on the team. You may get technical advice from people not on the team. All of the interviews and information should be kept as evidence for the team, but the people providing the evidence don’t need to be team members.
Training the Team (and Others)

A common belief is that “good people” naturally know how to investigate incidents. All they need to do is ask some questions and use their judgment to decide what caused the incident. Maybe they can ask “Why?” five times. Then they can use their creative thinking (brainstorming) to develop corrective actions. Have you ever experienced this approach? What did you think?
We don’t believe this haphazard approach works well. We’ve seen dramatic improvements in the ability of a team to effectively investigate an incident, find its root causes, and propose effective corrective actions when the team is trained appropriately BEFORE they start an investigation. This means selecting people and getting them trained before an incident occurs.
What kind of training do they need? Of course, more is better, but here is the minimum training we suggest…
- Team Leaders / Coaches – A course covering advanced root cause analysis, interviewing, and presentation skills. We suggest the 5-Day TapRooT® Advanced Root Cause Analysis Team Leader Course. Also, the Team Leaders should be well-versed in report writing and the company’s investigation policies. Coaches/facilitators should be familiar with facilitation skills/practices. Also, Team Leaders and Facilitations should continually upgrade their skills by attending the TapRooT® Summit.
- Team Members – A course covering advanced root cause analysis skills. We suggest the 5-Day course mentioned above or the 2-Day TapRooT® Incident Investigation and Root Cause Analysis Course or the 3-Day Virtual Course.
- People Involved in the Incident – It may seem strange to some that people involved in an incident need incident investigation training. However, we have observed that people are more cooperative if they understand the workings of the investigation process and techniques. They are more willing to cooperate when they understand that a TapRooT® Incident Investigation is not blame-oriented. Therefore, we recommend that all line employees take a 4-hour TapRooT® Basics course when TapRooT® is implemented across a site. We have developed and provided this training for many licensed clients who have found that it helps their investigation effectiveness.
- Management Training – This may be the most required and least understood training that needs to happen before an incident investigation. Leadership needs to know how TapRooT® Root Cause Analysis works, what resources an investigation team needs, and what their role in incident investigations and root cause analyses is. That’s why we created the TapRooT® Executive Leadership’s role in Root Cause Analysis Course. This course can be customized for your management and held at your site, or leadership can attend the pre-Summit course held on April 24-25, 2023, at the Margaritaville Lake Resort, Lake Conroe, near Houston, Texas. CONTACT US to schedule a course at your site.
Keep Your Team on Track
One real challenge for an investigation team leader is to keep their team on track.

Simple items include ensuring the right people perform interviews to collect information and that the information collected is documented and shared with the whole team.
The team leader needs to work with the team and allow enough discussion so that the team maintains a consensus about what happened, the incident’s causal factors, and the root causes of the causal factors. Different team members will start the investigation with different points of view and different experiences. Turf wars or finger-pointing can develop when these differences are not considered. This can be exacerbated when different team members perform different interviews and get just a few pieces of the puzzle.
Therefore, the team leader must have a plan to keep all the team members informed of the information collected and to build a team consensus as the investigation progresses. Frequent team meetings using the SnapCharT® to help build consensus can be helpful. Using the Root Cause Tree® Dictionary to guide the root cause analysis process helps the team come to an agreement about the root causes. The team leader should also make sure that the evidence that causes the team to select a root cause is recorded (this can be documented in the TapRooT® Software) so that when discussions of why a cause was selected occur, the evidence is readily available.
Learn More
There is much more to learn. Experienced team leaders have many stories to tell about the knowledge they have learned “the hard way” in performing team incident investigations. But you can avoid learning many of these lessons the hard way if you attend the TapRooT® 5-Day Advanced Root Cause Analysis Team Leader Course. See the upcoming public courses by CLICKING HERE.
If you have already attended a 5-Day TapRooT® Course, you can learn more about best practices at the TapRooT® Immersion Experience Track or the Advanced TapRooT® Skills Track at the 2023 Global TapRooT® Summit. CLICK HERE for more info about all the Summit Best Practice Tracks, and CLICK HERE for more information about the Summit Keynote Speakers.

This Has Been a “Best of” Article
This article has been updated and reprinted from the June 1994 Root Cause Network™ Newsletter, Copyright © 1994. Reprinted by permission. We think the information provided is just as timely as when it was originally written in 1994.