Runaway and derailment of wagons at Toton, Nottinghamshire
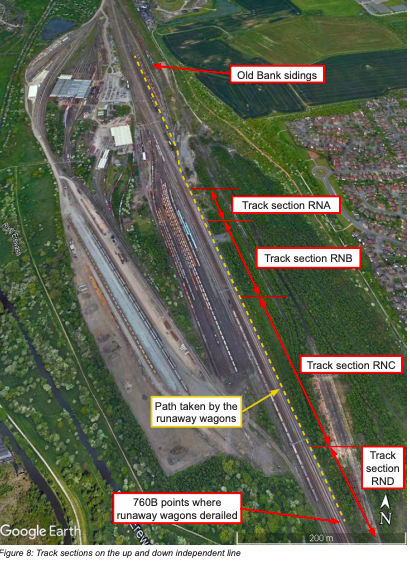
A Rail Accident Investigation Branch (RAIB) investigation of the runaway and derailment of wagons found multiple underlying factors contributing to the accident.
At 04:42 am on January 7, 2021, a rail wagon ran away from its course, leading to the derailment of wagons.
A rake (a series or a set) of 22 wagons, 21 of which were loaded, ran away from Old Bank sidings at Toton, Nottinghamshire, in the United Kingdom. As it pulled away and proceeded, the rake passed a red signal, which generated an alarm that alerted the signaler. The rake passed a second red signal and, a short distance later, the leading four wagons derailed at the end of the run-out rails associated with a set of trap points. The trap points worked as intended to derail the unauthorized movement. The leading two derailed wagons stopped foul of the adjacent running line, although no trains were nearby when the derailment occurred. The rake of wagons traveled a total distance of about 0.6 miles (1.0 km) during the runaway.
RAIB’s investigation found that the wagons ran away because no one had secured it with either handbrakes or scotches after it was stabled in Old Bank sidings the previous evening.
This meant that the wagons were only being held by air trapped in their brake systems, which subsequently leaked away.
The wagons were free to move because the incoming train they were part of had not been secured before its locomotive was uncoupled and because there was miscommunication between the ground staff on duty about who would secure the train.
An underlying factor was that staff at Old Bank sidings were routinely leaving trains unsecured for short periods of time, but this was not identified by DB Cargo’s safety assurance activities. A second underlying factor was that DB Cargo had no clear process in place that defined the tasks required when trains arrived, and no process to provide confirmation that these tasks had been carried out.
The consequences of the runaway were made potentially worse because the leading two wagons fouled the adjacent running line after derailing at the trap points. RAIB found that Network Rail’s risk assessment processes for both new and existing trap points only considered mitigations that were not applicable to uncontrolled runaway vehicles. These assessments also did not consider that runaway vehicles, once derailed, could travel as far as they did in this accident.
Recommendations
RAIB has made four recommendations.
- The first is that DB Cargo should establish the extent to which vehicles are being left unsecured in its yards and sidings, and identify and address the possible reasons for this.
- The second recommendation is that DB Cargo should review and improve its processes for trains arriving at its yards and sidings so it is clear when tasks should be undertaken, who is responsible for them and how their completion is communicated.
- The third recommendation is that DB Cargo should review its current arrangements for supervising, monitoring and auditing safety in its yards and sidings.
- The fourth recommendation calls on Network Rail to revise its risk assessment process for trap points, so that it considers the risk of an adjacent running line becoming fouled when uncontrolled vehicles run away.
RAIB also identified two learning points:
- The first reminds drivers and staff carrying out ground staff duties of the importance of securing vehicles prior to detaching locomotives.
- The second is a reminder that the primary purpose of trap points located on the exit from sidings, or on the exit of a goods line which connects to sidings, is to protect running lines from runaway vehicles.
Source: Rail Accident Investigation Branch (RAIB), “Runaway and derailment of wagons at Toton, Nottinghamshire, 17 January 2021,”
Safety and quality experts already know that TapRooT® Root Cause Analysis is the best tool to find human-performance-based root causes
TapRooT® RCA is the only system that uses scientifically derived root causes to eliminate bias and avoid blame. So, what are they missing? That Equifactor® Equipment Troubleshooting should be used WHENEVER there is an equipment failure.
Equifactor® equips the user with a series of predefined equipment troubleshooting tables. For example, there are tables for different types of pumps, AC and DC motors, refrigeration units, etc. These tables will give you a list of symptoms to choose from, and then provide an extensive list of possible causes for that symptom.
EQUIFACTOR® IS AN EFFECTIVE WAY TO GIVE YOUR MAINTENANCE AND RELIABILITY EXPERTS A VALID LIST OF POSSIBLE CAUSES TO BEGIN THEIR TROUBLESHOOTING EFFORTS.
So when would you use these Equifactor® Tables in your TapRooT® Investigation? The series of predefined equipment troubleshooting tables are obviously a great resource for an equipment failure incident. The tables give you a list of symptoms to choose from. However, don’t limit yourself to the obvious investigations. For example:
- You can also use Equifactor® during an injury investigation if one of your Causal Factors happens to be an equipment failure.
- Similarly, during an investigation of a Quality deviation, you may find a failure of a piece of equipment on the manufacturing line. Again, it could be employed to better understand the causes of the equipment failure (probably a Causal Factor), which will then lead to a better root cause analysis.
Use Equifactor® anytime an equipment failure is involved in your investigation. It’s an effective, efficient way to make sure you are fully covering all the possible errors and failures during your TapRooT® analysis.
Get the new book & a masterclass of learning in an Equifactor® Troubleshooting Course
The recently remastered 2-Day Equifactor® Equipment Troubleshooting & TapRooT® Root Cause Analysis Course comprises the complete package, as students receive the course, the new book, and the workbook. Take a look at the full course description.
Now is a great opportunity to get your maintenance personnel, equipment operators, and supervisors trained to increase equipment reliability at your plant.
We are excited to share with you the upcoming public Equifactor® courses. Reach out to us if you have any questions. To discuss on-site course arrangements, call us: 865.539.2139.