Significant Influx Taken During Managed Pressure Drilling (MPD) Operations
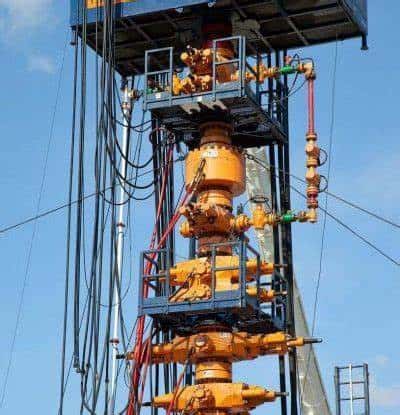
While drilling a deepwater exploration well, using an MPD setup, a significant influx was experienced.
Managed Pressure Drilling techniques offer the potential to optimize well designs or reduce NPT or even allow for safer drilling of a well but, like the introduction of any technology, tool, or process that is new to the team, it can also represent new risks that must be identified and addressed if the change is to be a successful.
In this instance, the well was successfully closed in. If just one or two actions had been different or perhaps just slightly slower the outcome may have been much more severe than just time spent recovering from an influx.
Significant influx taken during managed pressure drilling (MPD) operations
While drilling an exploration well with an MPD system, a rapid increase in well flow out was observed and the well was shut in. The well flow was measured at ~ 45 bpm and a gain of approximately 240 bbls was taken prior to shut in.
What went wrong?
A rapid increase in flow out was observed. Within 6 seconds, the flow out increased from the drilling rate of 1,600 gpm to in excess of 3,000 gpm. Within the MPD system setup, the Coriolis meter raw data was evaluated by the system to determine “good” data versus “bad” data. However, when performing this data validation step the Coriolis meter flow out threshold settings considered values less than 0 gpm and greater than 3000 gpm to be “bad” data.
In response to bad Coriolis meter data, the system would use for calculations and display a zero value
Due to this system response, the rig personnel were provided data indications that there was no flow out, when it actually exceeded 3,000 gpm, and the surface back pressure was observed to be increasing despite a fully opened choke. The initial diagnosis by the crew was a plugged choke.
In addition to providing the rig team with incorrect data, the response of the MPD system to a zero flow out value resulted in the kick detection logic not generating an alarm that a kick had been detected. The flow increased to a value in excess of the upper range limit, i.e. 3,000 gpm, at which point a zero-flow value was returned, in less time than the kick detection trending period of 20 seconds.
The MPD flow line tied into the rig flow line downstream of the rig’s conventional flow detection system and the mud logging equipment.
Corrective actions and recommendations for this drilling incident
- Understand if the MPD software includes logic to evaluate the raw data being received.
- Understand the MPD system logic and ranges and what responses occur when exceeding the defined ranges. This information must be considered during the HAZOP (Hazard and Operability) study and assure rig-based personnel understand the system response.
- Determine if conventional flow detection is available for MPD operations and if not, would this additional monitoring parameter provide value.
This Lesson Sharing report is from the IOGP Well Control Incident Subcommittee, IOGP WCI Lesson Sharing 21-6.
The TapRooT® System trains you to solve problems
Circumstances can crop up anywhere at any time if proper and safe sequence and procedures are not planned and followed. We encourage you to learn and use the TapRooT® System to solve problems.
TapRooT® has a team of investigators and instructors with years of extensive training ready to offer assistance worldwide. We also offer ongoing support to our clients through free newsletters and Root Cause Tip Videos, the Root Cause Analysis Blog, and our annual Global TapRooT® Summit.
Register for a TapRooT® course
Register for one of our courses. We offer a basic 2-Day course and an advanced 5-Day course.
Contact us, or call 865.539.2139 about having a course at your site or for further root cause analysis training opportunities. We’re here to find solutions for you.