When Subbing Out Work, Peruse, Verify, Follow All Aspects of Procedures
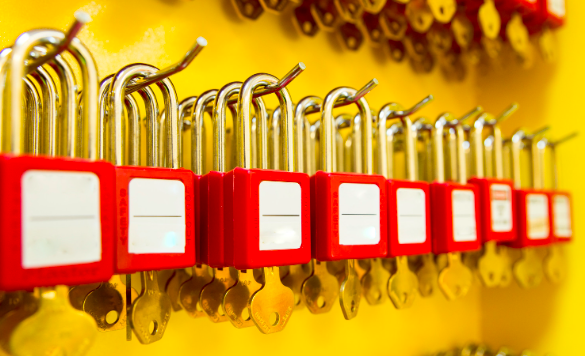
Pay close attention to agreements and procedures between subcontractors.
Following procedures is a make-or-break step in the subcontracting process. On 9/24/2019, a General Subcontractor (GC) assisted two sub-tier subcontractors on establishing a Lockout/Tagout (LO/TO) on a firewater post indicator valve (PIV) to allow them to work in an excavation. The procedure used to hang the locks was an approved GC owned procedure which was allowed due to an Interface Agreement between Battelle Energy Alliance (BEA) and the GC.
When procedures don’t match the physical circumstances
When the locks were hung, three of the sub-tier’s locks were attached to another lock and not a LO/TO device.
This created the situation when one of the individuals removed their lock three other locks came with it. In this configuration, there was no exclusive control for three individuals.
During the pre-job activities of 9/25/2019, it was identified that a LO/TO was needed once again to get into the excavation. One sub-tier expressed a concern to the Construction Field Representative (CFR) about the LO/TO. The CFR and a safety professional interfaced with the GC and reviewed their procedure.
Upon review and a subsequent discussion, it was identified that the 9/24/2019 LO/TO had not been performed per their procedure. At that time, a Stop Work was established for all LO/TO activities for the GC. When the last lock was removed from the PIV on 9/24/2019, all personnel were out of the excavation and no one went back into the excavation after the locks were removed, hence no one was exposed to a potential hazard.
Defining the issues that caused the problems
- Even though the LO/TO procedure was approved, the GC did not execute the elements of the procedure as is expected.
- The GC did not train staff or sub-tier subcontractor staff to the procedure as was required.
- When the first LO/TO was performed, none of the individuals questioned the way the locks were being installed. It was not until after work had been done under the LO/TO that questions were asked and the issue identified.
Lessons learned
When subcontractors have an Interface Agreement and can use their own approved LO/TO procedure. the following should occur:
- Before the first use of the procedure, all documentation should be checked to ensure that the subcontractor has performed the needed training.
- A review of the subcontractor’s equipment should be performed to ensure they have the proper LO/TO equipment to complete the LO/TO evolution.
- All subcontracted employees should understand the importance of and the need for them to utilize Stop Work authority.
- Verify all aspects of subcontractor-owned procedures prior to use.
Content source/credit: This Lesson Learned was distributed by OPEXSHARE and published by the Idaho National Laboratory, Idaho Falls, Idaho; reference number: CO 2019-2217.
Founded in 1988, the TapRooT® Root Cause Analysis System
solves hurdles every investigator faces
TapRooT® Root Cause Analysis Training System takes an investigator beyond his or her knowledge to think outside the box. Backed with extensive research in human performance, incident investigation, and root cause analysis, TapRooT® is a global leader in improved investigation effectiveness and productivity, stopping finger-pointing and blame, improving equipment reliability, and fixing operating problems.
System Improvements, the creator of the TapRooT® System, has a team of investigators and instructors with years of extensive training ready to offer assistance worldwide. We also offer ongoing support to our clients through free newsletters and root cause tip videos, the root cause analysis blog, and our annual Global TapRooT® Summit.
Register for a TapRooT® RCA Course
Register for one of our TapRooT® courses. Among all the TapRooT® Training courses, we offer a 2-Day TapRooT® Root Cause Analysis Course and a 5-Day TapRooT® Advanced Root Cause Analysis Team Leader Course.
Contact us or call us at 865.539.2139 about having a course at your site or for further root cause analysis training opportunities. We’re here to help you find solutions.