Do Lean Transformations Need Advanced Root Cause Analysis?
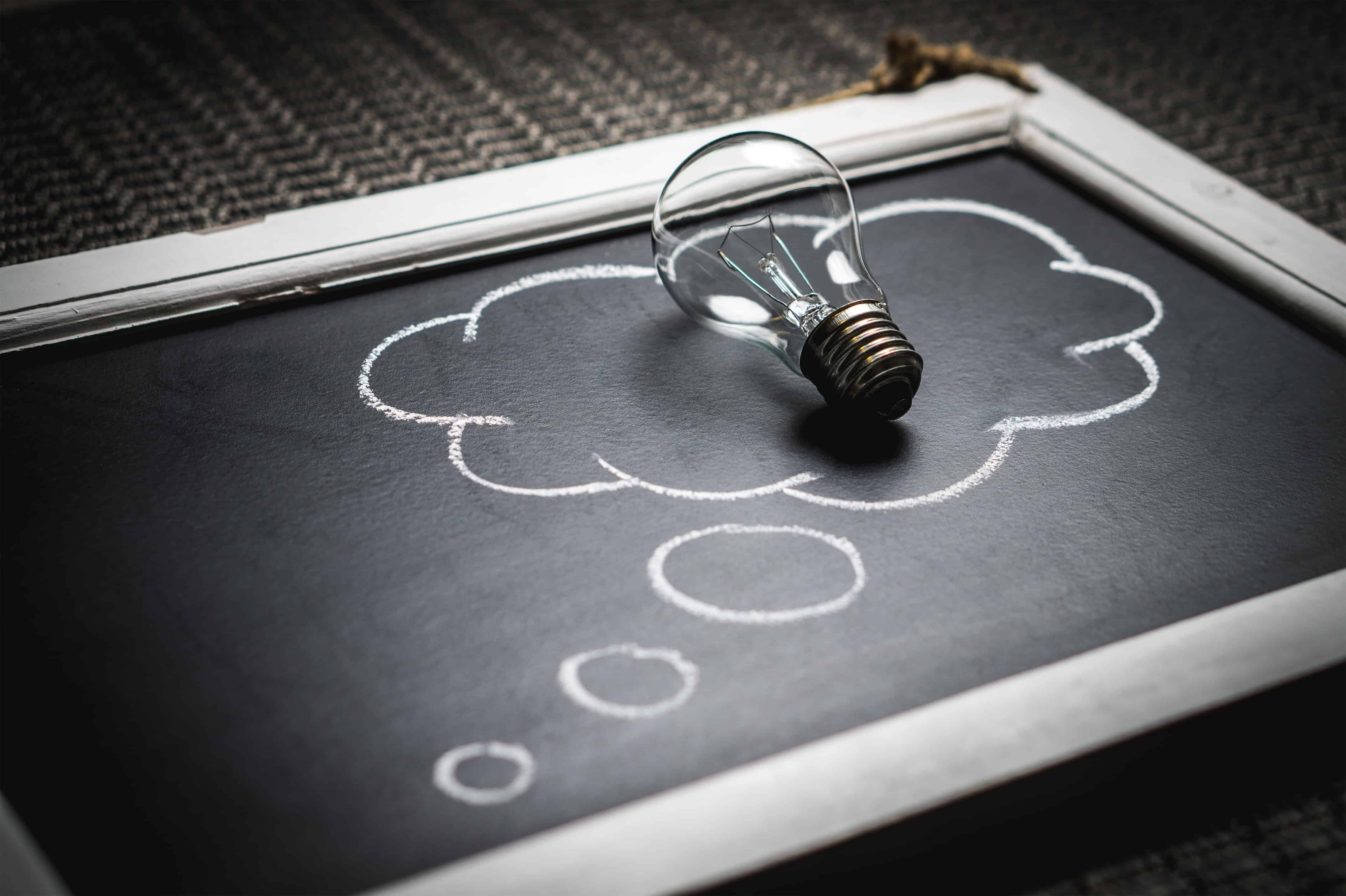
Lean Transformation and Root Cause Analysis
Since the authors of The Machine That Changed the World (1991) reintroduced the principles of Lean to the US, countless companies have tried to implement Lean principles and tools into their businesses. Most have failed to complete a Lean transformation, making temporary gains in productivity and quality, only to stagnate after three years.
Traditional Lean “Gurus” would tell you that failure to implement Lean is due to management commitment or cultural failure. The “Gurus” might say that leaders failed to take ownership of the process. However, I have seen organizations where the leaders and team members follow every Lean principle but still fail to achieve success.
Therefore, the question is:
What is the underlying flaw in the
modern approach to Lean transformation?
Improved Problem-Solving
One important Lean focus is making problems easily visible and having resources respond quickly to the problems (part of continuous improvement). Some companies believe that if people are made aware of problems, they will be able to find the problem’s root causes and fix them.
How do they find the problem’s root causes? The employees use their knowledge, and a simple root cause analysis technique (5-Whys, Fishbone diagrams, or the 8D methodology). The tools provide a structure to help employees display what they already know – the cause of the problem.
This system has a flaw. The employees must know every cause for a problem.
Lean problem-solving tools assume root cause analysis is an automatic process, and employees have the expertise (knowledge) to solve the problem using the structure of 5-Whys (or one of the other techniques). These systems rely on users knowing not just the answers to process questions but also what questions should they ask to find root causes.
But what if:
- Your employees don’t know all the ways the system can fail (they aren’t experts)?
- They don’t ask the necessary questions to uncover critical information?
- They are new to the process, department, or company?
When faced with the uncertainty of determining the root cause, nonexperts migrate toward biases and their comfort zones:
- Trainers will find problems with training.
- Quality professionals will find procedures that were not clear or not followed.
- Managers will find someone to discipline.
To a worker with a hammer, everything looks like a nail. You can build a house using only nails, just like you achieve initial improvements using classic lean tools. But eventually, you run out of low hanging fruit. Organization’s lean transformation improvements begin to plateau because of their investigators reach the limits of their knowledge.
Developing Better Problem-Solvers
How long would it take for your problem-solvers to become experts in human factors, mechanical failure, psychology, fatigue, procedure writing, and other disciplines?
Would you like your problem-solvers to have access to the knowledge needed to spot the causes of human errors, equipment failures, procedures problems, …?
There is a solution that provides an expert system to help your problem-solvers ask advanced questions to find root causes and develop effective corrective actions to stop repeat problems.
What system is it? The TapRooT® Root Cause Analysis System.
How does it work?
Come back next week for an example of how TapRooT® fits into the 8-step problem-solving process.
What if you can’t wait? Register for a TapRooT® Course and get started stopping your repeat problems once and for all. See the upcoming courses at:
https://www.taproot.com/store/Courses/