Comparing Common Root Cause Analysis Techniques (Updated)
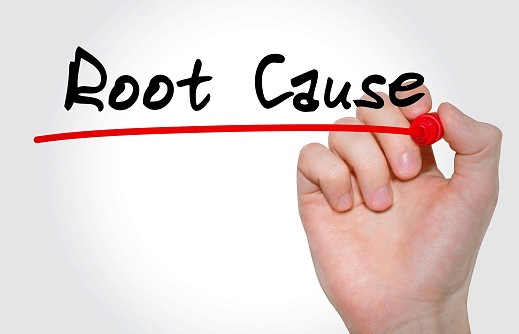
Comparing Root Cause Analysis Techniques
I’ve had so many people ask me, “How do you find a root cause?”, that I decided to put my best advice and the advice of others in one article to let people compare common root cause analysis techniques. I saved the best advice for last, so if you want to skip the bad advice, jump down the page to the “The Root Cause Analysis System You Should Be Using – TapRooT®” section.
This article will compare several root cause analysis techniques and suggest the right answer to make your root cause analysis program successful. Here are the main topics covered:
- 5-Whys – A “Simple” RCA Technique
- Fishbone Diagrams
- Fault Tree Analysis
- Failure Modes and Effects Analysis (FMEA)
- What’s Wrong with Cause And Effect?
- The Root Cause Analysis System You Should Be Using
- Conclusion – Pick the Right Root Cause Tool!
Here’s the video that sums things up … the article follows …
Simple RCA to More Complex to the Best
I’m going to start comparing root cause analysis techniques by presenting a common, “simple” root cause analysis technique – 5-Whys. A technique that I do NOT recommend (because it is too simple) but that I will share because it is frequently recommended by others. If you choose to use this simple technique, don’t blame me when the “root cause” you find and fix doesn’t seem to improve performance, and you keep having the same accidents happen over and over again.
Next, I’ll cover more complex techniques. Some of these are souped-up versions of the 5-Whys (other versions of cause-and-effect). However, the complex techniques – while being more complex – still have the same inherent problems as the simple technique. Therefore, I can’t recommend these more complex techniques for serious root cause analysis of important safety, quality, maintenance, service, or production issues.
Finally, I’ll talk about the technique you should be using – TapRooT®. A technique developed to avoid the problems presented by the previously mentioned simple and complex techniques. A technique that was intelligently designed to take you beyond your current knowledge. A technique that users praise for its repeatability, thoroughness, and effectiveness.
Before reviewing the techniques below, you may want to start by reading about the fundamentals of root cause analysis at THIS LINK.
5-Whys – A “Simple” Root Cause Technique
I’ve probably heard more expert root cause gurus talk about 5-Whys than any other root cause tool. Why? Because it is simple. Simple to teach and simple to use. All you have to do is ask “Why?” five times.

Here’s an example of the technique from the technique’s creator, Taichi Ohno (pictured above):
1. “Why did the robot stop?”
The circuit has overloaded, causing a fuse to blow.
2. “Why is the circuit overloaded?”
There was insufficient lubrication on the bearings, so they locked up.
3. “Why was there insufficient lubrication on the bearings?”
The oil pump on the robot is not circulating sufficient oil.
4. “Why is the pump not circulating sufficient oil?”
The pump intake is clogged with metal shavings.
5. “Why is the intake clogged with metal shavings?”
Because there is no filter on the pump. (root cause)
What do you think? Is “NO FILTER ON THE PUMP” a root cause? I think this example is a perfect example of what is WRONG with 5-Whys (and most unguided cause-and-effect analysis).
First, they missed a whole line of questioning. Why didn’t the loss of lube oil pressure trigger an alarm or an automatic shutdown?
Another line of questioning missed was, “Where did the metal shavings come from?” After all, metal shavings are not normally found in a well-maintained machine.
And finally, “Why was there no filter on the pump?” Did maintenance forget to install it? Did the designer fail to include it? Was it removed because it kept getting clogged?
All of these questions need to be answered, but the ultimate expert, Taichi Ohno, didn’t ask them because he probably thought he already knew the answer.
Want to see how the 5-Why example above compares to a TapRooT® Root Cause Analysis? CLICK HERE to see an article comparing TapRooT® to 5-Whys.
Watch this 5-Why training video and see if you can poke more holes in their example …
According to the video, you might need to ask why more or less than five times. And in other 5-Why training, they teach techniques to determine when you have asked enough “whys” to call the result a “root cause.” So asking why might not be so simple after all.
Watch this 5-Why example and see if you can tell when a root cause has been reached …
OK – that was a joke. But it demonstrates a problem with 5-Whys. How many whys are enough? Five, six, ten? Last week, I saw a 5-Why example with 17 whys. At that point (17 whys), 5-Why’s isn’t simple.
If you want to see more 5-Why examples, CLICK HERE. Then you will be fully trained in 5-Whys!
More Complex Root Cause Techniques
Many root cause analysis tools start with the idea of cause and effect. Every effect is caused. If you follow the cause-and-effect chain back far enough, you will reach the initial, root cause.
Most root cause gurus realize that an unguided 5-Why process fails to produce adequate results. Therefore, they modify the process by putting rules or structures around the asking of why (developing the cause and effect chain). They think rules or more extensive training can solve the basic defects inherent in cause and effect.
Here’s an article I wrote for Quality Progress (a quality-oriented professional society journal) that outlines most of the problems with cause and effect:
This video uses the same example (the bug example) that I critiqued in the Quality Progress article…
Sometimes people just keep repeating the same bad advice. It makes you wonder…
By the way, here is a blog post that completely debunks the bug example. The real analysis was a $2 million dollar study that took two years to complete (not somebody asking “Why?” five times) and led to a $25 million dollar corrective action program. The lighting change was tried and might have been successful, BUT it was not implemented because of tourist complaints. So much for a truthful example.
Fishbone Diagrams
Here is a training video about another cause-and-effect technique – a Fishbone Diagram…
Here’s what Dilbert has to say about Fishbone Diagrams …
http://www.dilbert.com/strips/comic/1993-08-27/
If you would like to read about the pros and cons of Fishbone Diagrams, CLICK HERE.
Fault Tree Analysis
Another common cause-and-effect analysis tool is “Fault Tree Analysis.” Here is a presentation demonstrating the technique to analyze a potential firewater failure …
Note: they didn’t include the potential for a broken line or a clogged strainer in their firewater failure example. Guess they didn’t think of that.
Failure Modes and Effects Analysis (FMEA)
Still another version of cause-and-effect used primarily as a design tool (rather than a root cause analysis tool) is Failure Modes and Effects Analysis (or FMEA). Here is a video about FMEA …
What’s Wrong with Cause-and-Effect for RCA?
For me, each cause-and-effect example presented above provides proof of why you should NOT use the technique for root cause analysis of incidents.
Why?
- First, the examples show that the technique simply displays the analysis team’s current knowledge. To be a good root cause analysis technique, the technique must help you go beyond your current knowledge. Cause-and-effect doesn’t get you there.
- Second, all the techniques suffer from a common cause-and-effect problem – CONFIRMATION BIAS. Read more about confirmation bias HERE and HERE.
- Third, the examples demonstrate another problem … the SINGLE CAUSE issue. Many times cause-and-effect (especially 5-Whys) only finds a single “root cause.” They miss the multiple opportunities to improve performance that you get when you identify all the root causes.
That’s a quick start to describe what’s wrong with cause-and-effect (all the techniques above). And as the old song says, “
For it’s one, two, three strikes, you’re OUT!
At the old ball game.”
The Root Cause Analysis System You Should Be Using – TapRooT®
Back in 1985, I started looking for a way that people in the field could be taught to find the root causes of human error and equipment failure-related incidents. Because of my human factors training, I often saw causes that others couldn’t see. I knew the answer wasn’t for me to do every investigation (the ultimate root cause guru) or to put everyone through the same training and experience that I had. Instead, the answer was to develop a system that would help people be able to troubleshoot, understand, and fix problems by leading them to root causes that they previously would have overlooked.
My work over the next six years eventually leads to the development of the TapRooT® Root Cause Analysis System. And that initial development work was just the start. The team at SI, with the help of tens of thousands of users, has continuously improved TapRooT® for over 30 years.
How does TapRooT® work?
Let’s start with THIS LINK that talks about root cause analysis fundamentals.
Next, see this WEBSITE PAGE (the “How Does TapRooT® Work?” description is 1/3 the way down the page).
Plus, here is a TV interview about TapRooT® Root Cause Analysis…
What’s the best way to learn to use TapRooT®? One of these courses:
- 2-Day TapRooT® Root Cause Analysis Training
- 2-Day Equifactor® Equipment Troubleshooting & TapRooT® Root Cause Analysis Training
- 5-Day TapRooT® Advanced Root Cause Analysis Team Leader Training
For those who want to investigate simple incidents and lead difficult, major investigations, I recommend the 5-Day TapRooT® Advanced Root Cause Analysis Team Leader Training.
Conclusion – Pick the Right Root Cause Tool!
I hope this article helped you understand and compare some of the techniques available to perform a root cause analysis and the limitations of cause and effect.
Please be careful when you decide on “How to find root causes.” Picking the wrong technique can lead to poor analysis and corrective actions that don’t solve the real root causes. Failure to fix the real root causes of problems could allow major accidents (fatalities, explosions, fires, …) to occur. That’s why we developed TapRooT® … because we know you really need to find and fix the root causes of serious safety, quality, production, service, or maintenance issues.
And you can be assured that you are making the right choice because TapRooT® Training is GUARANTEED:
Attend a TapRooT® Course, go back to work, and use what you have learned to analyze accidents, incidents, near-misses, equipment failures, operating issues, or quality problems. If you don’t find root causes that you previously would have overlooked and if you and your management don’t agree that the corrective actions that you recommend are much more effective, just return your course materials/software, and we will refund the entire course fee.

Mark – can I use the above link to reply to the various ‘safety differently’ and ‘safety 2’ proponents that invariably argue ‘RCA is useless’ based on a limited understanding of 5-Why and CAE? I get tired of arguing that ‘your characterisation of RCA as ineffective is because you’re using tools that are NOT RCA tools’.
Great idea Gary. Also try this link:
https://www.taproot.com/keepitsimple/
It discusses Safety II and TapRooT®.
I found out more information about the “bug” example and added it to this article.