Six Root Cause Analysis Bad Practices
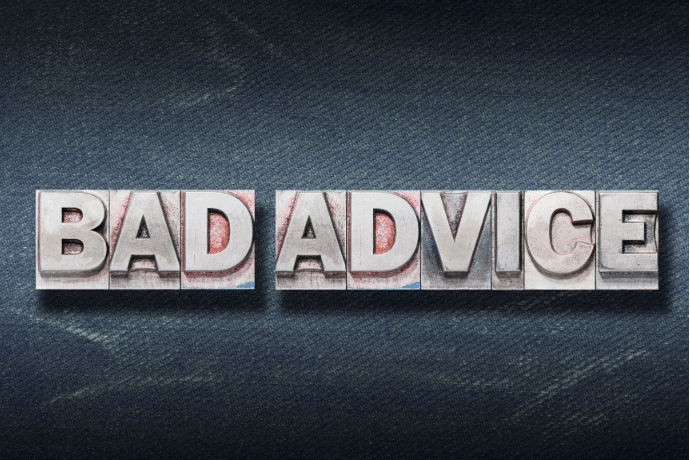
Are You Using Root Cause Analysis Bad Practices?
It’s surprising how many people I see providing bad advice when it comes to root cause analysis. Therefore, I started making a list of the root cause analysis bad practices that I see recommended or implemented. Avoiding these root cause analysis bad practices is a good start to improving your company’s root cause analysis program.
Root Cause Analysis Bad Practices
Let’s start with a simple list of the six root cause analysis bad practices and then we will expand on the details of each one…
- Failure to do root cause analysis
- Try to do too many root cause analyses
- Use bad root cause analysis tools
- Poor corrective actions
- No training for investigators
- No training for management
Failure To Do Root Cause Analysis
The simplest, and most common, root cause analysis mistake is not to perform a root cause analysis. You might think that this isn’t too common, but I see it all the time. People jump to conclusions and start with knee-jerk reactions based on assumptions. In fact, this may be the most common reaction when something goes wrong.
When do you see this happen?
- When equipment fails.
- When there is a “human error.”
- When a customer complains.
The obvious answer to fix this problem is to develop an effective policy of when to perform a root cause analysis that includes direction on the use of effective advanced root cause analysis techniques. Below is more about this.
Try To Do Too Many Root Cause Analyses
Sometimes people go overboard with root cause analysis. They start investigating problems that really aren’t worth investigating. Then people start taking shortcuts to save time completeing worthless investigations.
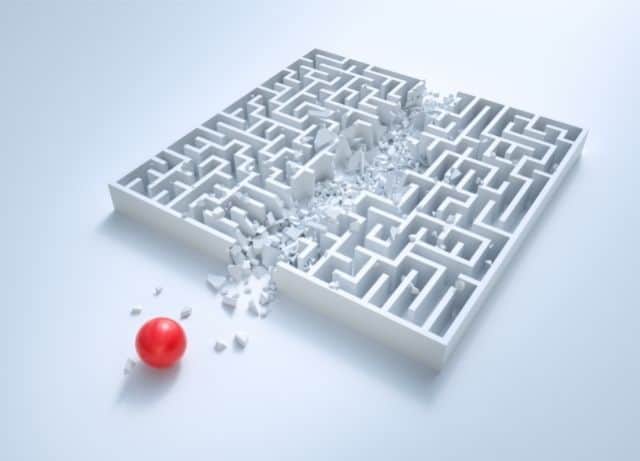
What are some examples of these “not worth investigating” incidents?
- Minor injuries with no real consequences that could NOT have become major injuries. (We call them “paper cut” injuries.)
- Minor equipment failures that just need the component replaced. (We call them “burnt-out bulbs.”)
- Minor process upsets that don’t cause significant production lost time, quality issues, or customer complaints.
What happens when you make people investigate problems that aren’t worth investigating? See this article…
Do you face this issue? Then you need to adopt a clear policy about what needs to be investigated and adopt the TapRooT® Root Cause Analysis System for low-to-medium risk incidents.
First, what does the TapRooT® System for low-to-medium risk incidents look like? See THIS LINK for more information.
Second, you need to develop criteria for what needs to be investigated. This should guide people to investigate important incidents and just record and trend paper cut incidents, burnt-out bulbs, and minor process upsets. These can be trended to see if a bad trend in these smaller incidents deserves a more complete investigation.
To find out more about writing a policy for investigations, see Book 2: TapRooT® Root Cause Analysis Implementation.
To learn more about trending, see Book 8: TapRooT® Performance Measures and Trending for Safety, Quality, and Business Management.
Use Bad Root Cause Analysis Techniques
To understand what is a bad root cause analysis technique, you need to understand what fundamentals are needed for good root cause analysis. See this link to find out about the fundamentals of good root cause analysis:
Fundamentals of Good Root Cause Analysis
What happens if you adopt a “too simple,” bad root cause analysis technique? See this article…
So, forget about 5-Whys, Fishbone Diagrams, Cause-and-Effect, and Blamestorming. It’s time you adopted a technique that can be used to effectively investigate simple and complex incidents: TapRooT® Root Cause Analysis.
Poor Corrective Actions
This is another common root cause analysis problem. People find one or more root causes, but they still can’t seem to fix the problems. They revert to the Three Standard Corrective Actions to fix all problems.
What are the three standard corrective actions?
- Discipline. This starts with the common corrective action: “Counsel the employee to be more careful when …”.
- Training. This may be the most used (and misused) corrective action of all.
- Procedures. If you don’t have one, write one. If you already have one, make it longer.
The misuse of these three standard corrective actions is the reason that so many accident investigations don’t really cause performance to improve. They don’t solve the real problems (the real root causes).
Another problem with corrective actions is the “Re” corrective actions. Examples?
- Re-train
- Re-write the procedure (without specific guidance on what to change)
- Re-mind the operator about a rule or a way to do something
- Re-emphasize (same as reminding)
- Re-place a part (unless you have decided it was a Tolerable Failure)
- Re-evaluate (why wait – evaluate now and suggest a fix)
- Re-view (same as re-evaluate)
- Re-qualify (a variation on retrain)
- Re-peat anything (a warning, training, an evaluation, …)
If these actions didn’t work the first time. what makes you think they will work when you try them again?
Think about this …
If it didn’t work the first time, why will it work this time?
Instead of using a “re”, why not fix the problem?
What caused the first training, procedure, part, rule, emphasis, or qualification to fail?
Consider using a more effective Safeguard or a corrective action higher on the hierarchy of safeguards:
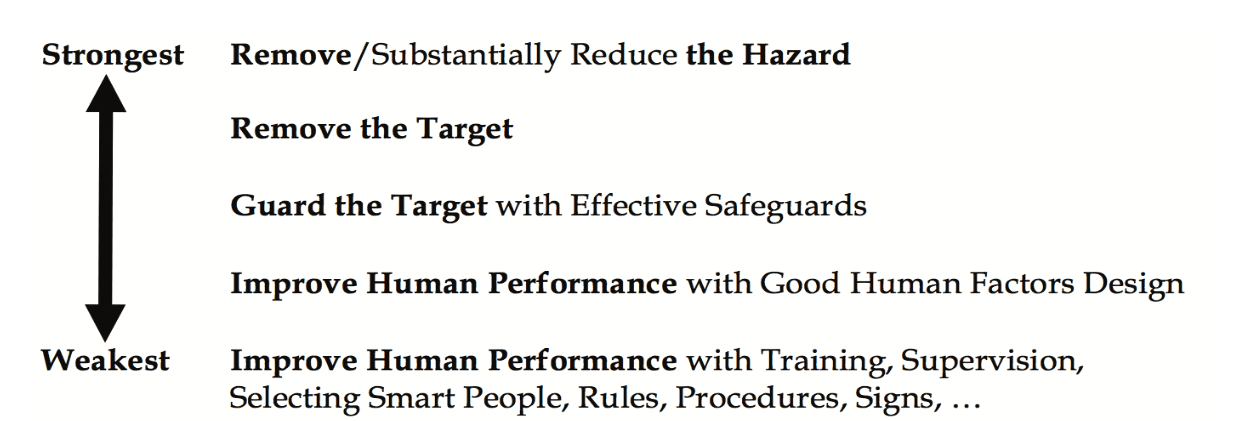
Or use the suggestions from the Corrective Action Helper® Guide!
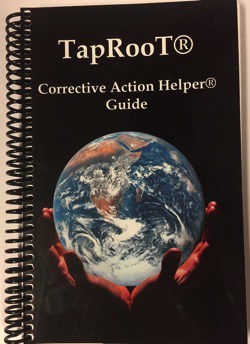
How many of your corrective actions fall into the three standard corrective actions or a “Re” corrective action? Have you audited or evaluated your past corrective actions? Most facilities will find the percentage of ineffective corrective actions is way above 50%, perhaps as high as 90%.
If you fix these corrective actions deficiencies, you might not have “Re”-peat incidents.
No Training for Investigators
How many times have I seen untrained investigators trying to find the root causes of human performance and equipment reliability problems? Too many to count.
Do your investigators know:
- How to investigate both simple and complex incidents and accidents?
- How to interview witnesses?
- How to collect evidence?
- How to analyze human performance issues?
- How to systematically troubleshoot equipment problems?
- How to develop the most effective corrective actions?
- How to present their investigations to management?
Perhaps they need effective root cause analysis training. See our TapRooT® Courses HERE. And have a look at the course outline for the 5-Day TapRooT® Advanced Root Cause Analysis Team Leader Training.
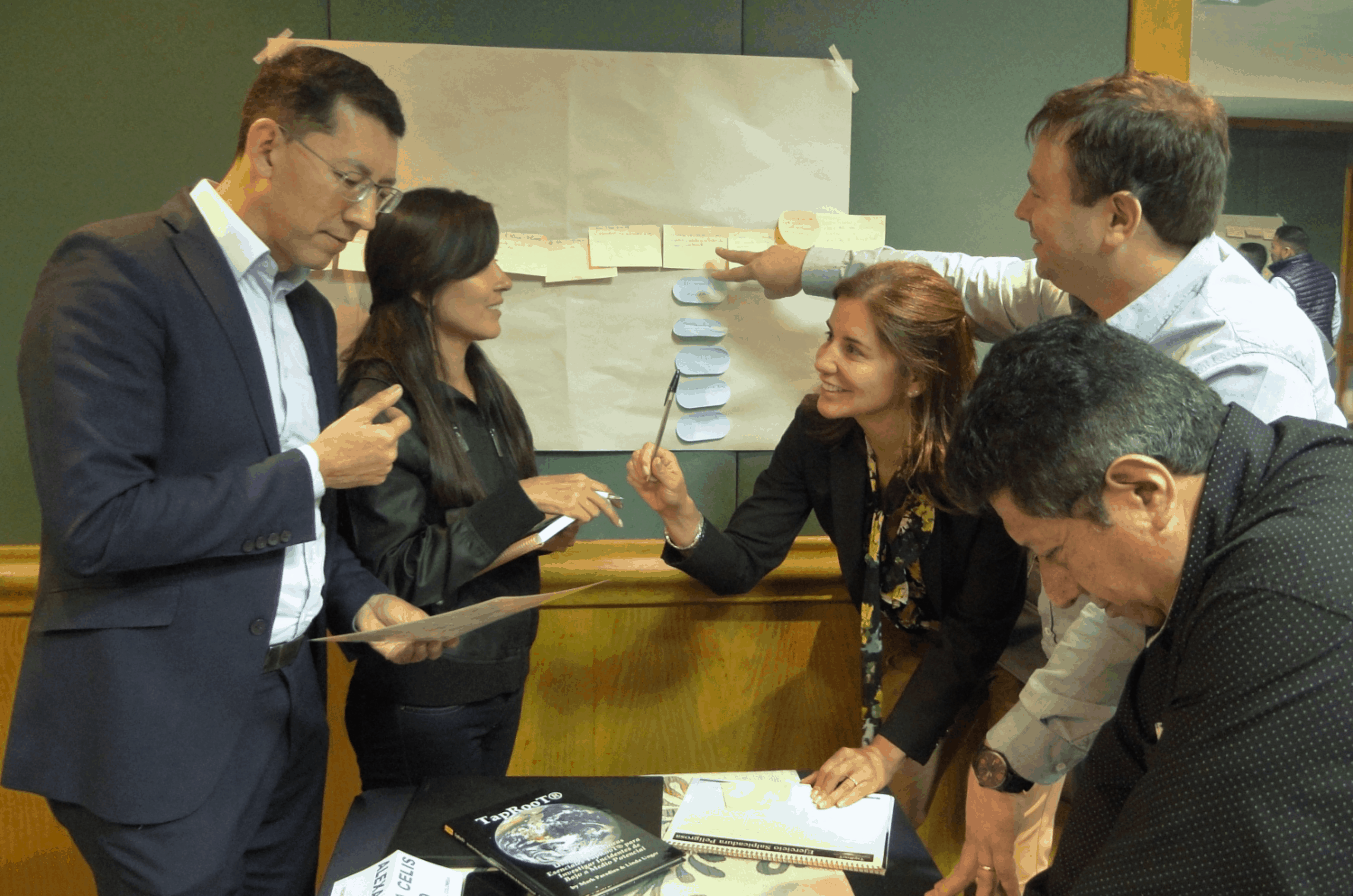
No Training for Management
What happens when management doesn’t understand root cause analysis and doesn’t understand their very important role in reviewing and approving investigations? Have you ever been asked by a manager to find a rock and then been told:
“Not that rock. Find me a different rock.”
Root cause analysis without agreed-upon definitions and processes can be a frustrating exercise.
How should your management be trained? See the outline for the TapRooT® Executive Leadership Course.
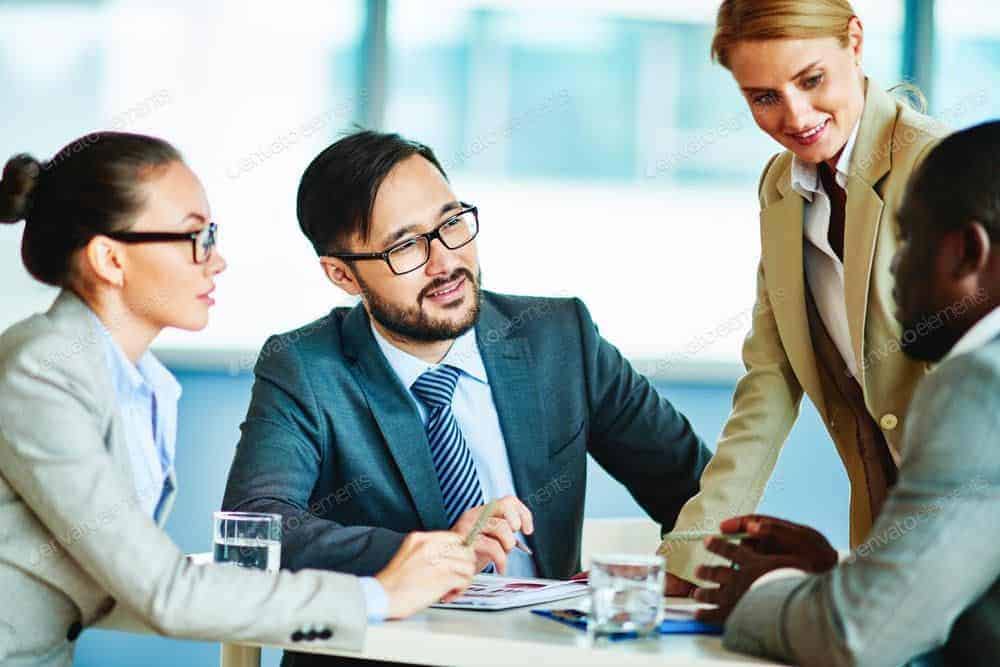
Get the Books or Attend the Classes
If you want to avoid the six root cause analysis bad practices and implement industry-leading best practices I would suggest these ideas…
First, Read the Books
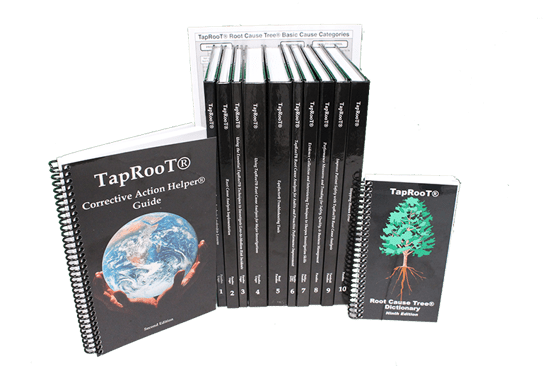
Which books? The whole 10 book set. See…
Next, Attend TapRooT® Training
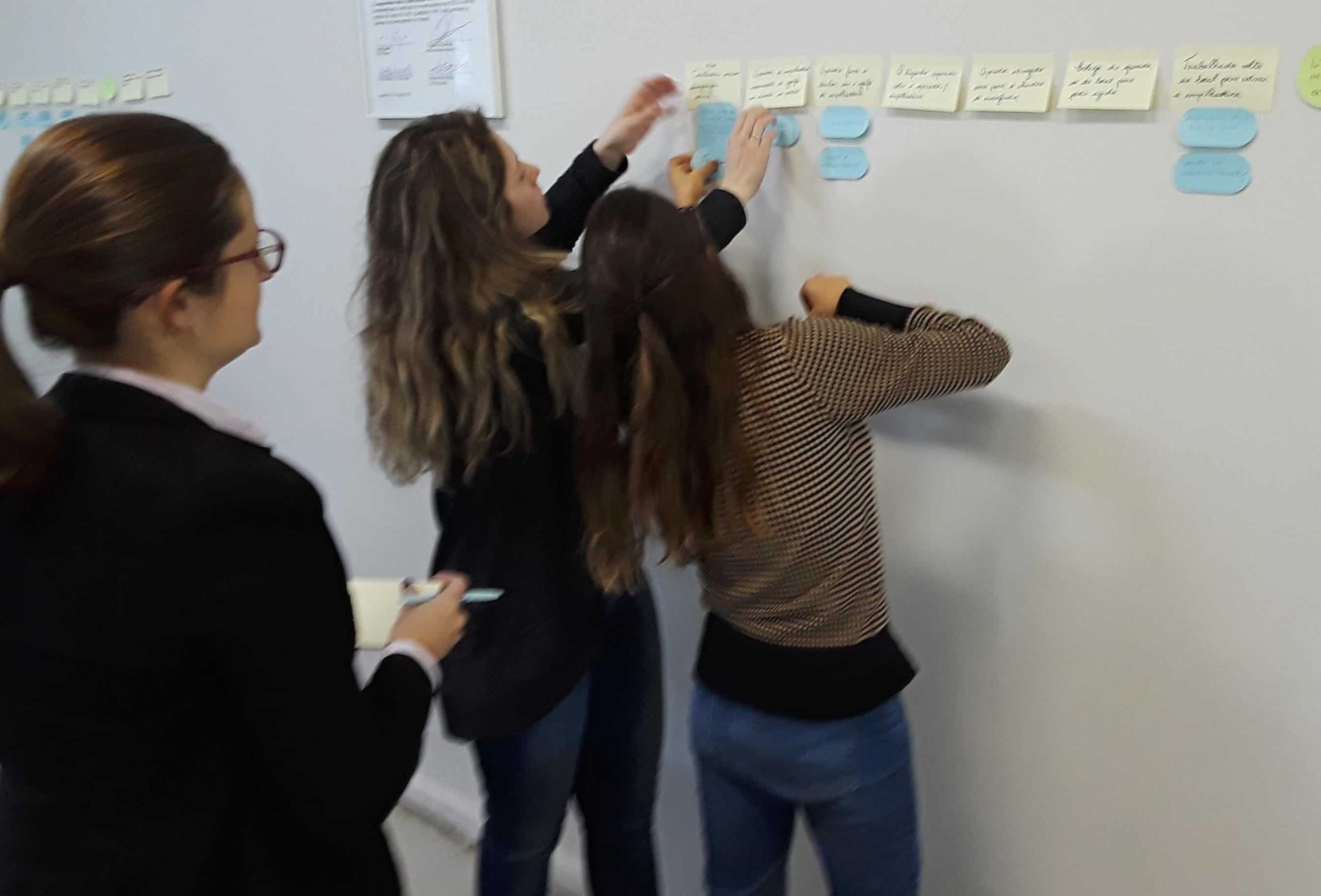
What training? There are several courses to choose from.
For a quick start, attend the 2-Day TapRooT® Root Cause Analysis Training or the 3-Day VIRTUAL TapRooT® Root Cause Analysis Training. See the course outline at the links above. See the upcoming public courses at the links below.
Upcoming 2-Day Root Cause Analysis Training
Upcoming 3-Day VIRTUAL TapRooT® Root Cause Analysis Training
For Advanced Team leader Training for both simple and complex incidents, attend the 5-Day TapRooT® Advanced Root Cause Analysis Team Leader Training. See the upcoming public courses at the links below.
Do you need to learn about the other courses we offer including management training, equipment troubleshooting, and the Stopping Human error Course? CLICK HERE.
Don’t wait. You can’t afford ineffective root cause analysis training and the impacts of the six root cause analysis bad practices. You need to get your root cause analysis upgraded to the industry’s best practices – TapRooT® Root Cause Analysis.
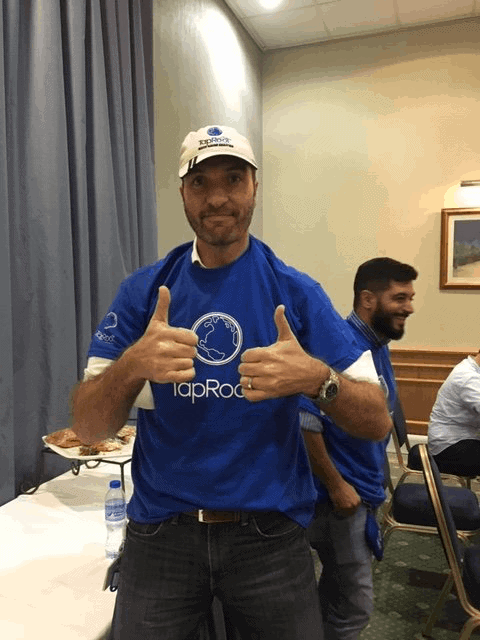