Why Human Error is NOT a Root Cause
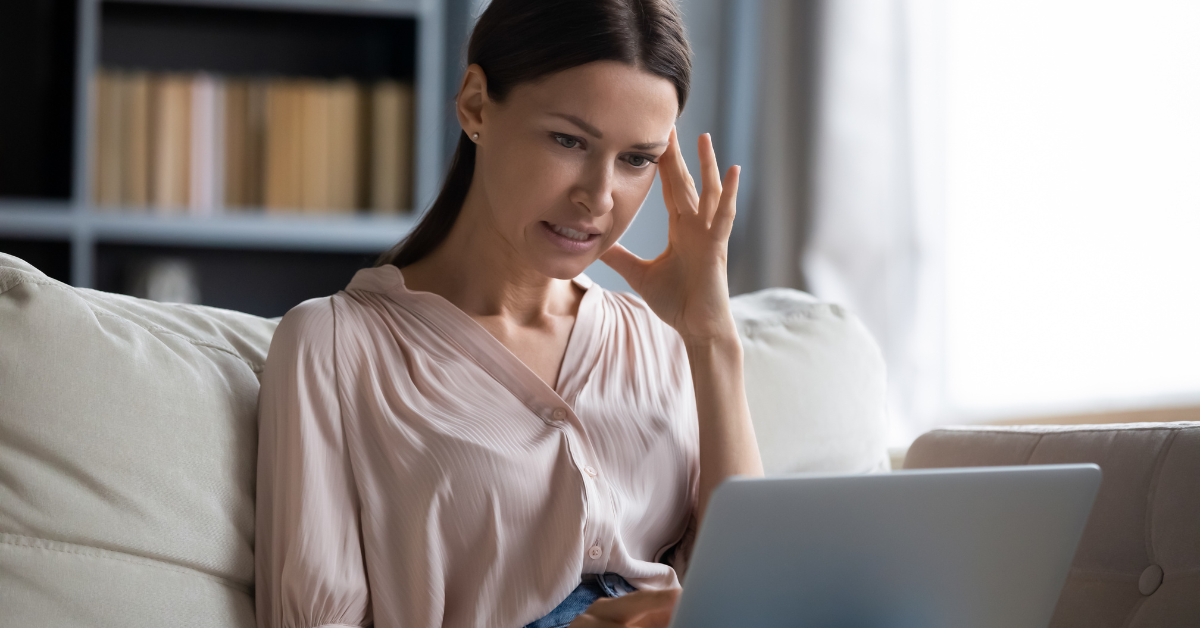
Human Error …
Not a Root Cause
Human Error: I’ve seen many incident investigations and quality root cause analyses conclude that “human error” is the root cause of their problem.

In this article, we will explore how you must go beyond human error to improve human performance and stop human error-related incidents and quality issues.
We will explore:
- Why human error is not a root cause
- Going beyond human error as a root cause
- How to find the root causes of human errors
- How to be proactive to prevent human errors
Read on to discover why human error is NOT a root cause and find proven ways to stop human errors.
Why Human Error is NOT a Root Cause

Before we explain that human error is not a root cause, we need to define the term “root cause.” The definition in the TapRooT® Books is:
“The absence of a best practice or the failure to apply
knowledge that would have prevented a problem.”
This is our most recent (modern) definition. For the history of our definition of a “root cause,” CLICK HERE.
Because a human error is NOT the absence of a best practice or the failure to apply knowledge that would have prevented a problem (as defined above), human error is not a root cause.
Instead, human error is better defined as a Causal Factor:
Causal Factor:
A mistake, error, or failure that directly leads to
(or causes) an Incident (the circle on the SnapCharT®) or
fails to mitigate the consequences of the original error.
Most human errors are a mistake, error, or failure. Thus, a human error is a Causal Factor – the point where TapRooT® Users start their root cause analysis. For more about the identification of Causal Factors, see:
Going Beyond Human Error as a Root Cause
How do you go beyond human error (beyond a Causal Factor)? First, you must get beyond BLAME.

This means you must leave the Blame Vision behind. For discussions about the Blame Vision, the Crisis Management Vision, and the Improvement Vision, see Book 1: TapRooT® Root Cause Analysis Leadership Lessons by Mark Paradies and Linda Unger. Order it by CLICKING HERE.
But how do you find the real root cause(s) rather than placing blame? That’s easy. You use the TapRooT® Root Cause Tree® to guide you to the root causes of human error-related incidents and quality issues.
What is the Root Cause Tree® and how does it work? It is an 8.5″ by 11″ guide (also implemented in the TapRooT® Software) that provides you with an expert system to find the root causes of human errors.

First, if there is a human error, the investigator identifies it as a “Human Performance Difficulty.” (We try to stay away from the term “human error” as that tends to lead to blaming.)
Answering the 15 questions leads the investigator to topics to investigate in more detail and reduces blame because it guides investigators to fixable root causes. An example of one of the 15 questions is:

The topics to investigate in more detail are called Basic Cause Categories. There are seven of them:
- Procedures,
- Training,
- Quality Control,
- Communications,
- Human Engineering,
- Work Direction, and
- Management Systems.
If a category is indicated by one of the 15 questions, the investigator uses evidence in a process of elimination and selection guided by the questions in the Root Cause Tree® Dictionary.

Usually, more than one Basic Cause Category is indicated as a possibility. The investigator uses evidence to work their way down the tree until root cause or causes are discovered under the indicated categories or until that category is eliminated. Here’s the Human Engineering Basic Cause Category with one root cause indicated (Lights NI).

The process of using the Root Cause Tree® was tested by users in several different industries including a refinery, an oil exploration division of a major oil company, the Nuclear Regulatory Commission, an airline, and a hospital system. In each case, the tests proved that the Root Cause Tree® helped investigators find root causes that they previously would have overlooked and improved the company’s development of more effective corrective actions.
Would you like to see some success stories written by TapRooT® Users? Click HERE.
Or watch this video…
Learn to Prevent Human Errors
Once the investigator (or team) has identified the root causes, they are ready to develop corrective actions to remove the Causal Factors (human error) and prevent the recurrence of the incident. TapRooT® provides ideas for each root cause in the Corrective Action Guide (the Corrective Action Helper® Module in the TapRooT® Software).
TapRooT® also helps the investigators identify Hazards and/or Targets that need to be removed to reduce risk.
The goal of the corrective actions is to reduce/eliminate human error or to improve the reliability of the system by making errors unlikely or easy to spot and correct before an incident happens.
To learn to find the real root causes of human errors, attend a TapRooT® Root Cause Analysis Course.
What Course Should You Attend?
The 5-Day TapRooT® Advanced Root Cause Analysis Team Leader Training is the course I would recommend. We hold public courses all over the world and we can hold one at your site. For information about holding a course at your site, contact us by CLICKING HERE. To see where we are holding public courses around the world, see this link:
https://store.taproot.com/5-day
Be Proactive Stopping Human Errors
You don’t have to wait for an accident or incident to apply root cause analysis to stop problems. The TapRooT® System can be applied proactively to improve human performance and stop human errors. We even wrote a book about how to do it:

For more information about the book, see this LINK.
Stopping Human Error Course
But wait … there’s more. We have a course to teach you the concepts explained in the book. Register for the Stopping Human Error Course.
Stop blaming people and start finding the real root causes as soon as you can. Register for one of our courses TODAY!

In the field of safety management in my country, human errors are the most commonly cited “root” cause of major or minor incidents. The term of human performance is a taboo.
its is true Human Errors are no Root Cause, what baffles me is how Humans (people) contribute to over 80% cause to an incident.
People cause incidents, a lot of them with full knowledge (experience on routine and specific tasks), trained and re-trained, but still people cause incidents.
How do you then balance this fact?
That’s the topic of the Stopping Human Error Course. See: https://www.taproot.com/course/stopping-human-error-course/
I enjoyed your article!
Good article. I would go one step further on the reason for never stopping at Human error. In the construction field if we stop at human error we stop a blaming. If we place blame on one person the next person will not communicate any potential issues from fear of Quality Control “placing blame/Human error” on them.Human Error is not the stopping point but a point that has to be shown for education purposes. Human’s by nature do not want to create errors.. errors created by humans are likely due to lack of knowledge of some fashion..
Great point!
Good insight. Completely true that we should not stop at “human error” and probe further to arrive at the root cause. And it is usually possible. Only then system level improvements can be realized.
Mark:
What distinction do you make between a mistake, error, or failure, on one hand, and intentional violation, on the other? Intentional violation is a broad category that might be related to anything from widespread cultural issues (squarely in the Management System category) to a single bad actor with a disregard for requirements. Where does the latter case go on the tree and at what point would it become a root-cause?
I think this will answer your question: https://www.taproot.com/followup-why-human-error-is-not-a-root-cause/.
I had an older article with more details but I can’t find it (it may have been in the paper newsletter days).
Human error could be because of many contributory factors. if investigated deeply, root cause can be lead towards the organizational factors. the task factors, peer pressure, inadequate illumination, lack of supervision and many such factors will determine the root cause of an human error is due to organizational factors.
A follow on article: https://www.taproot.com/followup-why-human-error-is-not-a-root-cause/
So if not human error, what would it be when an experienced employee executes a manual task repeatedly day after day correctly, slips up once, misses a step, fails to recognize the mistake, then continues to perform the task again correctly over and over again under the same conditions. It obviously isn’t a knowledge gap or work environment problem. How to explain?
Good question.
In TapRooT® RCA, first you would draw a SnapCharT® of what happened and identify the Causal Factors (I see at least 2). You would then takes these to the Root Cause Tree® to find the root causes.
That would lead to the explanation.
Thanks
Mark